جرم نسوز چیست و چرا کوره اکسیژن قلیایی (BOF)، به آن نیاز دارد؟
کنورتور یا کوره اکسیژن قلیایی (BOF)، یکی از انواع کورههایی است که در صنعت فولاد و آهن، مورد استفاده قرار می گیرد. در کنورتور یا کوره اکسیژن پایه (Basic Oxygen Furnace)، به آهن مذاب تولید شده در کوره بلند، اکسیژن دمیده میشود تا امکان تولید فلز و پالایش آهن به بهترین شکل فراهم شود. کوره اکسیژن قلیایی مانند دیگر انواع کورههای موجود در صنعت فولاد و آهن، میتواند گرما و دمای بسیار زیادی را تولید کند، این حرارت و در کنار آن تنشهای مکانیکی و شیمیایی وارده، میتواند صدمه زیادی را به فیزیک و ویژگیهای مکانیکی کوره اکسیژن قلیایی وارد کند، تا حدی که ممکن است عملکرد آن به دلیل شدت آسیب وارده، متوقف شود. جرم یا توده نسوز در کوره اکسیژن قلیایی (BOF)، محصولاتی نسوز از خانواده بزرگ دیرگدازها هستند که که به دلیل داشتن ترکیبات خاص، قدرت تحمل حرارت بالا، مقاومت در برابر تنشهای مکانیکی شدید و حملات شمیایی مخرب، را ارائه میهند. بدین منظور، استفاده از جرمهای نسوز در لایههای مختلف تشکیل دهنده بدنه کوره اکسیژن قلیایی، میتواند آن را در برابر گرمای شدید ناشی از مذاب آهن و فعل و انفعالات شیمیایی آن، مقاوم سازد. به علاوه، اجرای جرم نسوز در بخشهای مختلف کوره اکسیژن قلیایی، باعث میشود تا این کورهها بتوانند در برابر واکنشهای شیمیایی فرآیند فولادسازی، مقاومت بالایی از خود نشان دهند. جرمهای نسوز استفاده شده در کوره اکسیژن قلیایی معمولا بر پایه منیزیا هستند؛ اما سایر ماتریسهای دیرگداز یا نسوز که مقاومت بالایی در برابر حرارت دارند نیز میتوانند مورد استفاده قرار گیرند.
پیشنهاد برای مطالعه
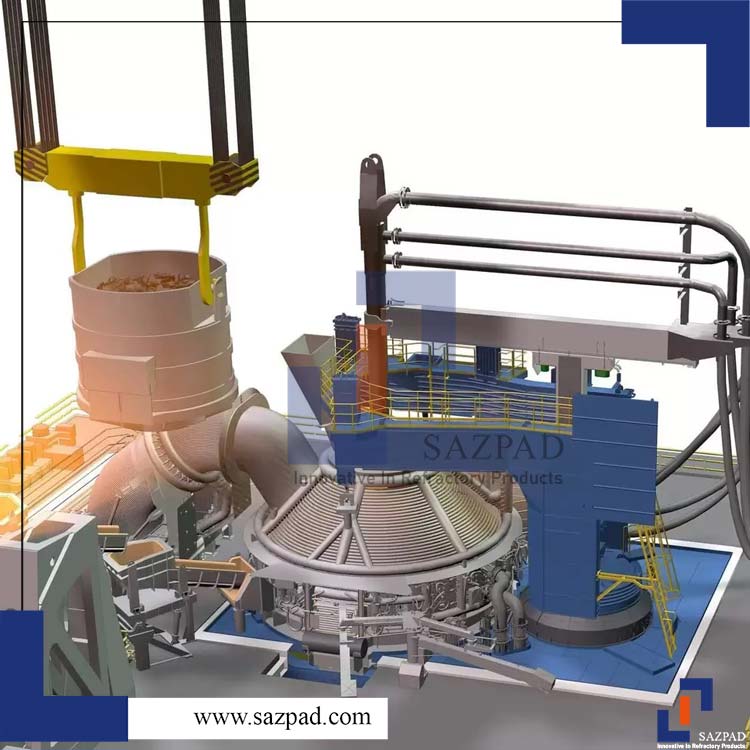
انواع جرم نسوز در کوره اکسیژن قلیایی
جرم نسوز کوره اکسیژن قلیایی باید مقاومت بالایی در برابر گرما و واکنشهای شیمیایی داشته باشد. چرا که کوره اکسیژن قلیایی، دقیقا جایی است که دمش اکسیژن، دمای کوره را به مراتب بالا برده و در کنار آن نیز، مذاب با شدت بالا تلاطم میکند. کوره اکسیژن قلیایی، از نگاه آنالیز TMC (Thermal , Mechanical and Chemical Analysis)، در حین عملیات پالایش مذاب آهن، شرایط شدید حرارتی، مکانیکی و شمیایی را تجربه میکند. پس جرمهای نسوز مورد استفاده در کنورتور یا کوره BOF، باید به صورت تخصصی برای مقابله با شرایط موجود در حین عملیات کوره اکسیژن قلیایی، انتخاب شوند. به طور کلی، جرمهای نسوز مناسب برای استفاده در کورههای اکسیژن قلیایی، در چند گروه مختلف طبقه بندی میشود که از جمله آنها، میتوان به موارد زیر اشاره کرد:
جرم نسوز سیمانی
یکی از انواع جرم نسوز رایج در کنورتور یا کوره اکسیژن قلیایی، جرم نسوز سیمانی یا همان سیمان نسوز است. سیمان نسوز، از مواد نسوز اولیه سیمانی، یعنی کلسیم و آلومینا تشکیل شده است. به طور کلی، تودههای نسوز سیمانی در پنج دسته به شرح مخلوط نسوز پر سیمان، ماتریس نسوز سیمان متوسط، مخلوط نسوز کم سیمان، توده نسوز فوق العاده کم سیمان و جرم نسوز بدون سیمان، تقسیم بندی میشوند که هر کدام ویژگی های خاص خودشان را دارند. در کورههای اکسیژن قلیایی (BOF)، به دلیل دمای بالا، شوک حرارتی زیاد، تنشهای مکانیکی و تنشهای شیمیایی مخرب، جرمهای نسوز کم سیمان و جرمهای نسوز بدون سیمان، در بین دسته سیمانهای نسوز، میتوانند بهترین انتخاب برای استفاده در بدنه کوره اکسیژن قلیایی باشند. چرا که، جرمهای نسوز با محتویات کمتر سیمان، به مراتب انعطاف پذیری بیشتر و مقاومت به حرارت بالاتری را ارائه میدهند.
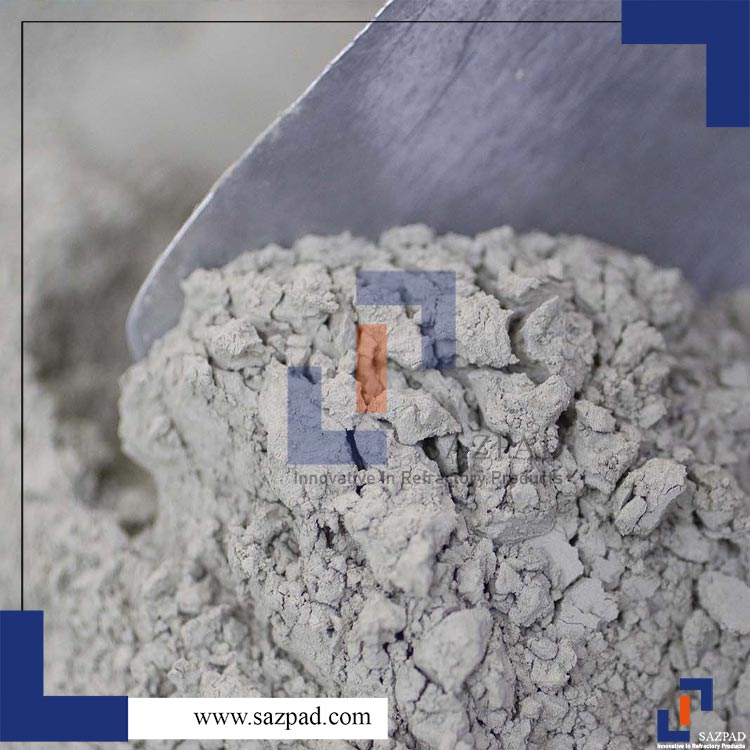
جرم نسوز سیلیسی
ماتریس نسوز سیلیسی از ترکیب 90 درصد دیاکسید سیلیکون (SiO₂) و در کنار آن، منیزیا و آلومینا تولید میشود. اگرچه جرمهای سیلیسی دارای مقاومت خوبی در برابر شوک حرارتی هستند، اما دیگر انواع مواد و محصولات نسوز مانند جرمهای نسوز کم سیمان (Low-Cement Refractory Mass) و جرمهای دولومیتی به دلیل مقاومت بالاتر در برابر این شرایط ترجیح داده میشوند. کنورتور یا کوره اکسیژن قلیایی (Basic Oxygen Furnace)، به دلیل استفاده از مواد قلیایی، محیطی قلیایی دارد. جرمهای نسوز سیلیسی در محیطهای قلیایی عملکرد خوبی ندارند و ممکن است دچار خوردگی و کاهش عمر مفید شوند. به علاوه، کوره اکسیژن قلیایی (BOF)، نیاز به مواد نسوزی دارد که در برابر سایش مکانیکی ناشی از شارژ مواد اولیه و حرکت مذاب مقاومت بالایی داشته باشند. جرمهای سیلیسی ممکن است مقاومت کافی در برابر سایش مکانیکی را نداشته باشند. همه اینها، به معنی عدم کاربرد جرمهای نسوز سیلیسی در کورههای اکسیژن قلیایی نیست. جرمهای نسوز سیلیسی، عمدتا در نواحی که حرارت نسبتا پایینتر است و با محیط قلیایی در تماس مستقیم نیستند قابل استفاده است. استفاده از جرمهای نسوز سیلیسی در بخشهایی نظیر نازلهای گازدمی، به چشم میخورد. استفاده از جرم نسوز سیلیسی در کوره های القایی در صنعت فولاد نسبت به کوره اکسیژن قلیایی یا BOF، بسیار متداولتر است.
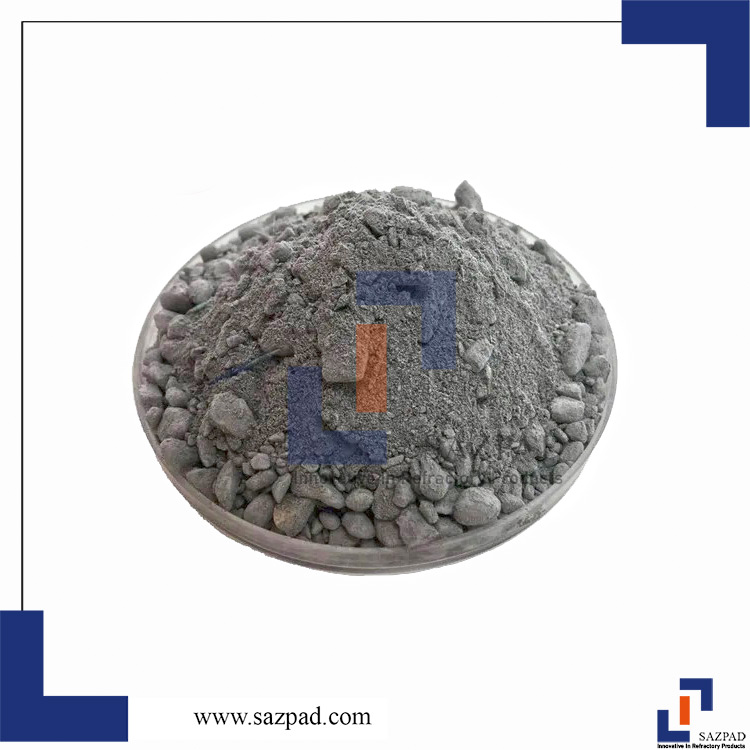
جرم نسوز آلومینایی
یکی دیگر از انواع توده دیرگداز کارآمد در کنورتور یا کوره اکسیژن پایه (BOF)، که معمولا نقش بسیار مهمی را در بهبود عملکرد کورهها ایفا میکند و قیمت آن نیز ارزان است، جرم نسوز آلومینیایی است. اساس ترکیب جرم نسوز آلومینایی را آلومینا (Al₂O₃) تشکیل میدهد. در کنار آلومینا، عناصر نسوز دیگری چون منیزیا، سیلیس و همچنین افزودنیهایی نظیر سیلیکات کلسیم، در اجزای تشکیل دهنده جرمهای نسوز آلومینایی، جای دارند. جرم نسوز آلومینایی (Alumina Refractory Mass) در کوره اکسیژن قلیایی (Basic Oxygen Furnace یا BOF) به طور ویژه کاربرد دارد. ماتریس نسوز آلومینایی به دلیل ویژگیهای مکانیکی خاص، در برخی بخشهای کوره اکسیژن پایه یا کوره BOF که نیاز به مقاومت بالا در برابر دما و شرایط سخت عملیاتی دارند، استفاده میشود. جرم نسوز آلومینایی، عمدتا به عنوان پوشش نسوز یا آستر نسوز در دیواره و کف کوره اکسیژن قلیایی که مستقیما با مذاب و شرایط سخت موجود، در تماس هستند، به کار گرفته میشوند. کاربرد جرمهای نسوز آلومینایی در صنعت آهن و فولاد، تنها به کنورتور یا کوره اکسیژن قلیایی یا BOF، ختم نمیشود. مزایای ویژه جرمهای نسوز آلومینایی سبب شده تا استفاده از آن در انواع تجهیزات در معرض حرارت صنعت آهن و فولاد، به طور گسترده دیده شود.
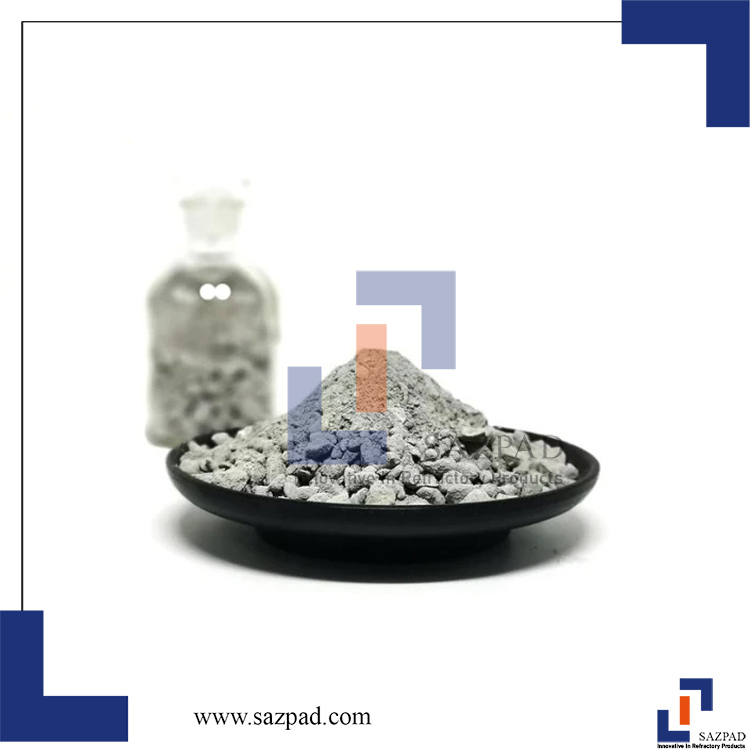
پیشنهاد برای مطالعه
جرم نسوز منیزیتی
متداولترین نوع توده دیرگداز در کوره اکسیژن قلیایی (BOF)، جرم نسوز منیزیتی یا منیزیایی (Magnesia Refractory Mass) است. بیشتر محتوای جرم نسوز منیزیایی، از عنصر نسوز منیزیا تشکیل شده است. در ترکیبات مخلوط نسوز منیزیایی، محتوا آلومینا، سیلیس و… نیز استفاده میشود. آنها به عنوان عنصر نسوز کمکی، رفتار حرارتی، مکانیکی و شیمیایی نسوزهای منیزیایی را ارتقا میدهند. توده نسوز منیزیایی (MGO)، دارای نقطه ذوب بسیار بالا است و میتواند دماهای بسیار بالا را تحمل کند. به علاوه، توانایی تحمل تغییرات سریع دما را نیز دارد. ماتریس نسوز منیزیایی، در برابر فشار، سایش و دیگر تنشهای مکانیکی موجود، به خوبی عمل میکند. از همه مهمتر، جرمهای نسوز منیزیایی، از پایداری شیمیایی عالی بهره میبرند. آنها در برابر محیطهای قلیایی و مواد قلیایی مقاومت بسیار خوبی دارند که این ویژگی برای استفاده در کوره اکسیژن قلیایی بسیار مهم است. علاوه بر این، طول عمر مفید بالا در جرمهای نسوز منیزیایی، سبب شده تا به عنوان، انتخاب عالی برای کورههای اکسیژن قلیایی محسوب شود. جرم نسوز منیزیایی، در دیواره و کف کوره اکسیژن پایه (Basic Oxygen Furnace)، یعنی دقیقا جایی که در تماس مستقیم با مذاب داغ، تنشهای مکانیکی و شیمیایی شدید است، قابل استفاده است.
توجه !! تمامی جرمهای نسوز سیمانی، جرم نسوز آلومینایی، جرم نسوز سیلیسی و جرم نسوز منیزیایی نام برده شده، به عنوان جرم نسوز ریختنی، جرم نسوز پاششی، مخلوط نسوز پوششی، ماتریس نسوز شاتکریت و جرم نسوز کوبیدنی، طراحی، تولید و به بازار عرضه میشوند. در واقع، طرح اختلاط، دانهبندی عناصر نسوز و ترکیبات تشکیل دهنده جرمهای نسوز، با هدف تامین ویژگیهای حرارتی، مکانیکی و شیمایی در توده نسوز و با در نظر گیری نوع روش اجرای جرم نسوز، تعیین و طراحی میشود. طبقهبندی جرمهای نسوز بر اساس روش اجرای آنها، امکان استفاده راحت و متناسب با هر ناحیه از کوره BOF یا کنورتور را فراهم میسازد. در کوره اکسیژن قلیایی (Basic Oxygen Furnace)، انواع جرمهای نسوز ریختهگری نسبت به دیگر تودههای دیرگداز، بیشتر مورد استفاده قرار میگیرند.
اگر به دنبال شناخت بیشتر از جرمهای نسوز ریختنی و کاربرد آنها در صنعت آهن و فولاد به خصوص در کوره اکسیژن پایه یا قلیایی هستید، به شما توصیه میکنیم تا مقاله ” جرم نسوز ریختهگری چیست و در صنعت چه کاربردی دارد؟ ” را مطالعه کنید و از آن بهره ببرید.
نقش انالیز TMC در بهینه سازی انتخاب جرم نسوز کوره اکسیژن قلیایی
ماتریس نسوز در کوره اکسیژن قلیایی بسیار متداول بوده و با توجه به ماهیت تولید حرارت بسیار زیاد در این کورهها، حتما باید مورد استفاده قرار گیرد. آنالیز TMC یکی از انواع آزمایشاتی است که برای انتخاب جرم نسوز کوره اکسیژن قلیایی و دیگر تجهیزات صنایع در معرض حرارت، انجام میشود. آنالیز TMC (Thermal , Mechanical and Chemical Analysis)، قابلیتهای جرم نسوز را از جنبههای مختلفی چون ویژگیهای حرارتی، مکانیکی و شیمیایی، مورد بررسی قرار میدهد. در ادامه، هرکدام از آنالیزهای TMC، به طور عمیقتر مورد بحث و ارزیابی قرار گرفته است :
- آنالیز TMC برای بررسی رفتار حرارتی توده نسوز : این آنالیز این امکان را به مهندسین میدهد تا رفتار توده نسوز در کوره اکسیژن قلیایی را در شرایط حرارتی مختلف مانند دمای بالا و نرخ های گرمایش مختلف مورد بررسی قرار دهند. برای شناخت خواص حرارتی مواد نسوز میتوان از این آنالیز کمک گرفت.
- آنالیز TMC برای بررسی رفتار مکانیکی ماتریس نسوز : آنالیز TMC یکی از انواع آنالیزهایی است که رفتار مکانیکی جرم نسوز در کوره اکسیژن قلیایی در شرایط فشاری و مکانیکی را بررسی میکند. در واقع، آنالیز مکانیکی توده دیرگداز (Mechanical Analysis)، تمامی خصوصیات مکانیکی توده دیرگداز یا نسوز مانند مقاومت در برابر کشش، مدول الاستیسیته و سختی توده دیرگداز را بررسی میکند.
- آنالیز TMC برای بررسی شیمیایی مخلوط نسوز : انتخاب جرم نسوز کوره اکسیژن قلیایی حساسیت بسیار زیادی دارد. زیرا، در کوره اکسیژن قلیایی، محیط قلیایی است و جرم یا مواد نسوز مورد استفاده در چنین محیطی یا باید از خاصیت شمیایی خنثی بهره ببرد و یا باید خاصیت قلیایی داشته باشند. آنالیز شیمیایی ماتریسهای نسوز (Chemical Analysis)، با بررسی انواع جرمهای نسوز و تطبیق آن با شرایط حاکم بر کوره اکسیژن پایه یا کنورتور، میتواند در انتخاب بهترین نسوز برای استفاده در کوره BOF، کارآمد باشد.
پیشنهاد برای مطالعه
اثرات جرم نسوز بر عملکرد کوره BOF و کیفیت محصولات آن
استفاده از ماتریس نسوز در کوره اکسیژن قلیایی (BOF)، به طور مستقیم بر عملکرد و رفتار حرارتی، مکانیکی و شیمیایی کوره اکسیژن پایه، تاثیر گذار است. توده نسوز، اگر چه تنها جزء تشکیل دهنده کورههای اکسیژن قلیایی نیست، اما میتوان ادعا داشت که اساسیترین و نقش آفرینترین جزء تشکیل دهنده کوره اکسیژن قلیایی، جرم نسوز است. ماتریس یا مخلوطهای دیرگداز، به عنوان آسترنسوز و یا پوشش نسوز، عمدتا سرتاسر قطعات و نواحی مختلف کوره اکسیژن قلیایی را میپوشانند. لاینینگ دیوارهها و کف کوره اکسیژن قلیایی با جرم نسوز، عملکرد بهینه کوره را فراهم میکند. پایداری و عمر مفید آن را تضمین میکند. از توقف تجهیزات در حین عملیات، جلوگیری میکند. با تعمیرات جزئی، امکان بازگشتن سریع کورههای BOF آسیب دیده را به خط تولید، فراهم میسازد. توجه داشته باشید که شرایط پایدار حرارتی، مکانیکی و شیمیایی کوره اکسیژن قلیایی، مسلما بر کیفیت نهایی محصولات تولید شده از BOF، بی تاثیر نیست. از پررنگترین اثرات جرم نسوز بر عملکرد کوره اکسیژن قلیایی (BOF) و کیفیت محصولات نهایی آن، میتوان به موارد زیر اشاره نمود :
افزایش مقاومت کنورتور در برابر خستگی حرارتی
در کوره اکسیژن قلیایی، حرارت و شوک حرارتی بسیار زیاد است. از این رو، جدارهها، سقف و کف کوره اکسیژن قلیایی، باید بتواند در برابر شکستهای ناشی از حرارت و تغییرات آن، مقاوم باشد. ماتریس نسوز در کوره اکسیژن قلیایی نقش بسیار مهمی را در افزایش مقاومت کوره BOF در برابر خستگی ایفا میکند. به طوری که، این مخلوط نسوز میتواند از پیشرفت خستگی در کوره جلوگیری کند. در واقع، جرمهای نسوز، با مقاومت بالا در برابر خستگی حرارتی، از وقوع این نوع شکست و ترک خوردگی، در دیواره، سقف و کف کنورتور یا کوره اکسیژن پایه، جلوگیری میکند. این امر باعث افزایش عمر مفید کوره و کاهش نیاز به تعمیرات مکرر میشود.
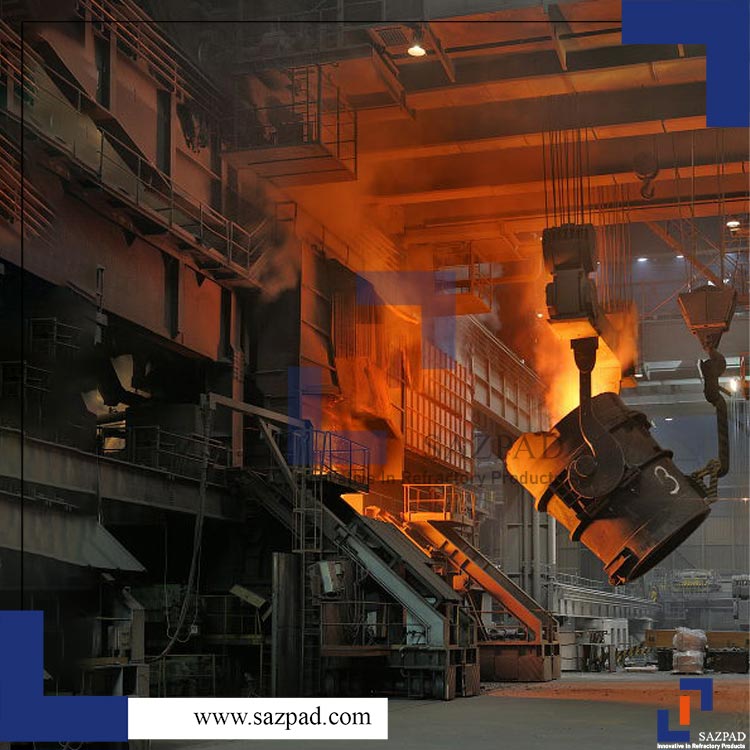
افزایش مقاومت کوره اکسیژن قلیایی در برابر خوردگی
در کوره اکسیژن قلیایی، فعل و انفعالات شیمیایی زیادی به منظور پالایش مذاب آهن و تبدیل آهن به فولاد خالص، رخ میدهد. از این رو، کنورتور یا BOF، در حین عملیات، همیشه در معرض حملات شمیایی و خوردگیهای ناشی از آن است. از این رو، مسلم است که در کوره اکسیژن قلیایی، باید برای مقابله با شرایط خشن شیمیایی حاکم، تدبیری اندیشید. این استفاده از جرمهای نسوز در پوشش داخلی کنورتور یا کوره اکسیژن پایه است که از بدنه کوره اکسیژن قلیایی را در برابر واکنشهای شیمیایی و خوردگیهای ناشی از آن، محافظت میکند. ماتریسهای دیرگداز، با مقاومت بالایشان در برابر خوردگی و تنشهای شیمیایی، از آسیبدیدگی ناشی از واکنشهای شیمیایی در دماهای بالا، جلوگیری میکنند. در واقع، تودههای نسوز، با ایجاد لایههای محافظ بر سطح داخلی کوره، مانع از تماس مستقیم مواد خورنده با دیواره کوره میشوند.
بهبود هدایت حرارتی در کوره اکسیژن قلیایی
حرارت، مهمترین نیاز کوره اکسیژه قلیایی برای فعالیت است. بیشترین بازدهی از کوره اکسیژن پایه، زمانی حاصل میشود که حرارت به طور یکنواخت در سرتاسر کوره، توضیع شود. جرمهای نسوز با هدایت حرارتی ویژه خود، این نیاز کوره اکسیژن قلیایی را به خوبی برآورد میکنند. ماتریسهای دیرگداز، با توزیع یکنواخت حرارت، اختلاف دما در نقاط مختلف کنورتور را کاهش میدهند. با کاهش اختلاف دما، شوک حرارتی که میتواند از عوامل مهم شکست و ترک خوردگی باشد، به مراتب کاهش مییابد. از طرفی دیگر، اتلاف انرژی به حداقل میرسد، مصرف سوخت به منظور تامین حرارت مورد نیاز کوره BOF، کاهش مییابد. بهبود هدایت حرارتی در کوره اکسیژن قلیایی به وسیله جرم نسوز، میتواند کیفیت و ظرفیت تولید محصولات نهایی کنورتور را افزایش دهد.
کنترل واکنشهای الکتروشیمیایی در کوره اکسیژن قلیایی
در حین شرایط عملیاتی کوره اکسیژن قلیایی، سلهای خوردگی شامل آند و کاتد، تولید میشود. در این سلها، واکنشهای اکسیداسیون و کاهش رخ میدهد که میتواند منجر به خوردگی اجزای کوره شود. از سوی دیگر، در تولید فولاد در کنورتور( کوره اکسیژن قلیاییBOF)، یونهای مختلفی نظیر کلسیم، منیزیم و آلومینیوم، در حین عملیات، به وجود میآیند که در صورت واکنش با اکسیژن و دیگر عناصر، اکسیدها و نمکهای قلیایی را تشکیل میدهند. به علاوه، در کوره اکسیژن قلیایی، گازهای خورنده متنوعی چون CO، CO2 و O2 تولید میشوند که میتوانند به صورت الکتروشیمیایی با دیوارههای کوره واکنش دهند. جرمهای نسوز با مکانیزمهای مختلف، واکنشهای الکتروشیمیایی را کنترل میکنند. از آنجایی که، جرمهای دیرگداز قادر به انتقال یونها و الکترونها هستند، میتوانند در فرآیندهای الکتروشیمیایی نقش داشته باشند. قابلیت هدایت الکتریکی کنترلشده در جرمهای نسوز، جریانهای الکتریکی ناخواسته را که میتوانند واکنشهای الکتروشیمیایی را تحریک کنند، کاهش میدهد. در واقع، تودههای دیرگداز، با جذب و تثبیت یونهای مخرب، از تأثیرات منفی واکنشهای الکتروشیمیایی جلوگیری میکنند. جرمهای نسوز به عنوان استر یا پوشش محافظ، انتقال گازها و یونهای مخرب را محدود میکند. در کنار تمام این قابلیتها، مقاومت شیمیایی بالای عناصر تشکیل دهنده ماتریس نسوز و همچینن، پایداری حرارتی و مکانیکی جرمهای نسوز، میتواند به کنترل واکنشهای الکتروشیمیایی و در پی آن، افزایش عمر مفید کوره BOF کمک کند.
پیشنهاد برای مطالعه
بهبود خواص مکانیکی فولاد تولید شده در کنورتور
استفاده از جرم یا ماتریس نسوز مناسب در کوره اکسیژن پایه (Basic Oxygen Furnace)، میتواند با فراهم سازی شرایط پایدار حرارتی، مکانیکی و شیمیایی، خواص مکانیکی و کیفیت محصولات نهایی کنورتور را، افزایش دهد. توجه داشته باشید که حتی نوع جرم نسوز مورد استفاده در نواحی مختلف کوره BOF، نحوه توزیع و اجرای جرم نسوز و همچنین نحوه عمل آوری آن نیز، در تنظیم خواص مکانیکی محصول نهایی کوره اکسیژن قلیایی یعنی فولاد، تاثیر گذار است. هر چه خواص حرارتی، مکانیکی و شیمیایی جرم نسوز منطبقتر با نیازهای موجود در کوره اکسیژن قلیایی باشد، مسلما شرایط پایدارتری در کوره BOF، ایجاد میگردد. از این رو، فولاد با کیفیت بالاتری نیز تولید خواهد شد. جرمهای نسوز، خواص مکانیکی فولاد، به خصوص مقاومت آن در برابر ضربه، مقاومت به کشش و سختی را تنظیم خواهند کرد.
کاهش تمرکز تنشها در کوره اکسیژن قلیایی
در کنورتور، حرارت به شدت بالا است. از طرفی، دمش اکسیژن نیز در حین فرآیند کوره اکسیژن قلیایی، قدرت تنشهای حرارتی را به مراتب افزایش میدهد. از این رو، بهترین راه حل برای حفظ کوره BOF، توزیع یکنواخت حرارت در سطوح داخلی کنورتور است. استفاده از جرمهای نسوز مناسب کوره اکسیژن پایه، با توزیع یکنواخت تنشهای حرارتی و مکانیکی در دیواره و کف کوره، از تمرکز تنش در نقاط خاص، جلوگیری میکند. این مزیت تودههای نسوز، باعث کاهش خطر ترکخوردگی و شکست در ساختار کوره میشود.
کاهش هزینههای تعمیر و نگهداری
جرم یا ماتریسهای نسوز کوره، با حفاظت همه جانبه از ساختار کوره، در برابر تنشهای حرارتی، مکانیکی و شیمیایی، وقوع آسیبهای احتمالی، شکست و ترک خوردگیهای ناشی از شرایط خشن کوره را به حداقل میرسانند. جرم نسوز کوره، با مزایای بی شمار خود، به عنوان پوشش نسوز و محافظ، عملکردی پایدار را در کوره BOF و دیگر انواع کوره صنعتی، فراهم میکند. علاوه بر این، جرمهای نسوز از قابلیت ترمیم و تعمیر سریع بهره میبرند. یعنی میتوان آسیبهای پدیدار شده را چه به طور موضعی و چه به طور کلی در سریعترین زمان ممکن تعمیر و ترمیم نمود. جالب است بدانید، جرمهای نسوز کوره را میتوان حتی در حین عملیات یعنی در زمانی که دمای کوره بالا است، بدون نیاز به خارج شدن کوره از خط تولید، تعمیر نمود. از طرفی جرمهای نسوز با هدف کمترین نیاز به تعمیر و نگهداری طراحی میشوند. بنابراین، استفاده از جرمهای نسوز کوره، هزینههای تعمیر و نگهداری کورههای اکسیژن قلیایی را به مراتب کاهش میدهند.
انواع کاربرد جرمهای نسوز در کوره اکسیژن قلیایی
کوره اکسیژن قلیایی، دستگاهی برای تولید فولاد است که در آن فلز غنی از کربن یا آهن خام توسط این کورهها به فولاد تبدیل میشوند. در کوره اکسیژن قلیایی، اکسیژن با درصد خلوص بیش از 99.5 درصد با سرعت زیاد به آهن مذاب دمیده میشود. با این کار، کربن و سیلیکون موجود در فلز داغ، اکسید خواهد شد و در نهایت مقدار زیادی گرما آزاد میکند که ضایعات مختلف را ذوب خواهد کرد. گرمای تولید شده در کوره اکسیژن قلیایی، میتواند صدمه زیادی به جداره کوره وارد کند و باعث آسیب جدی در آن شود. از این رو، در کوره اکسیژن قلیایی (BOF)، مخلوط یا ماتریسهای دیرگداز یا همان جرم نسوز در قطعات و اجزای مختلف کوره، مورد استفاده قرار میگیرد تا از دوام و عملکرد بهینه کنورتور اطمینان حاصل شود. استفاده از مخلوط یا ماتریسهای دیرگداز در کوره اکسیژن قلیایی از اهمیت بسیار زیادی برخوردار است. از این رو کاربرد جرم نسوز در کوره اکسیژن قلیایی بسیار زیاد است. در اینجا، تنها به پررنگترین موارد استفاده از ماتریسهای نسوز در کنورتور، اشاره شده است. موارد استفاده تودههای نسوز کوره، به شرح زیر است:
استفاده از جرم نسوز در بدنه کوره اکسیژن قلیایی (shell of the Basic Oxygen Furnace)
بدنه کوره اکسیژن قلیایی، اساس ساختار اصلی کوره را تشکیل میدهد. پس برای استفاده از کوره، حفظ عملکرد کوره و دستیابی به بیشترین حد بهرهبردای از آن، تامین پایداری و دوام بدنه کنورتور در حین عملیاتهای کوره اکسیژن پایه، اولویتی بسیار مهم است. از این رو، بدنه کنورتور، به آستر یا پوششهای نسوز و محافظ نیاز دارد تا بتواند در حین عملیات کوره BOF، تنشهای حرارتی، مکانیکی و شیمیایی مخرب وارده را تحمل کند و از وارد شدن آسیب به ساختار اصلی کوره، جلوگیری کند. پوششهای نسوز، همان جرمهای نسوز یا ماتریسهای دیرگداز هستند که با روشهای مختلف، بدنه کوره اکسیژن قلیایی را میپوشانند. جرم نسوز منیزیایی و جرم نسوز آلومینایی و انواع آجرهای نسوز مبتنی منیزیا و آلومینا، از رایجترین ماتریسهای دیرگداز بی شکل و جرمهای نسوز شکل دار مورد استفاده در بده کوره اکسیژن پایه، محسوب میشوند.
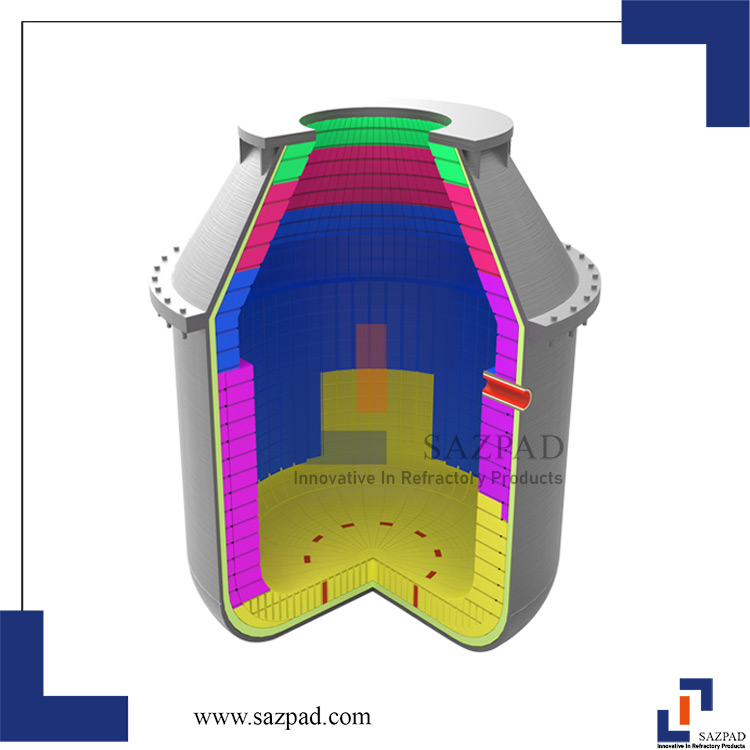
استفاده از جرم نسوز در دیوارههای جانبی (Side walls of the Basic Oxygen Furnace)
دیوارههای جانبی کوره اکسیژن قلیایی، جزئی مهم از بدنه کوره BOF هستند که به طور مستقیم با حرارت، ضربه، سایش و تنشهای مکانیکی و انحلالهای شیمیایی ناشی از عملیاتهای کوره، در تماس هستند. پس، اگر جداره جانبی کوره BOF برای مقابله با شرایط سخت موجود طراحی و آماده نشوند، مسلما نتیجه خوبی را در حین عملیات، ارائه نمیدهند. حتی میتوان گفت، در چنین وضعیتی کوره اکسیژن پایه، عملا کارایی ندارد. از این رو، استفاده از انواع جرمهای نسوز مونولیتیک و یا اجرای آجرهای نسوز و دیگر جرمهای نسوز شکل دار در دیواره جانبی کوره اکسیژن قلیایی، راه حلی رایج و کارآمد برای محافظت و تقویت دیواره جانبی در برابر شدیدترین دماها و خوردگیها و تنشهای مکانیکی کوره BOF، میباشد. پوشش دهی دیوارهای جانبی کنورتور با ماتریسهای نسوز یا اجرای قطعات نسوز پیش ساخته در آن ناحیه، طول عمر مفید و دوام دیواره جانبی کنورتور را به مراتب افزایش میدهد.
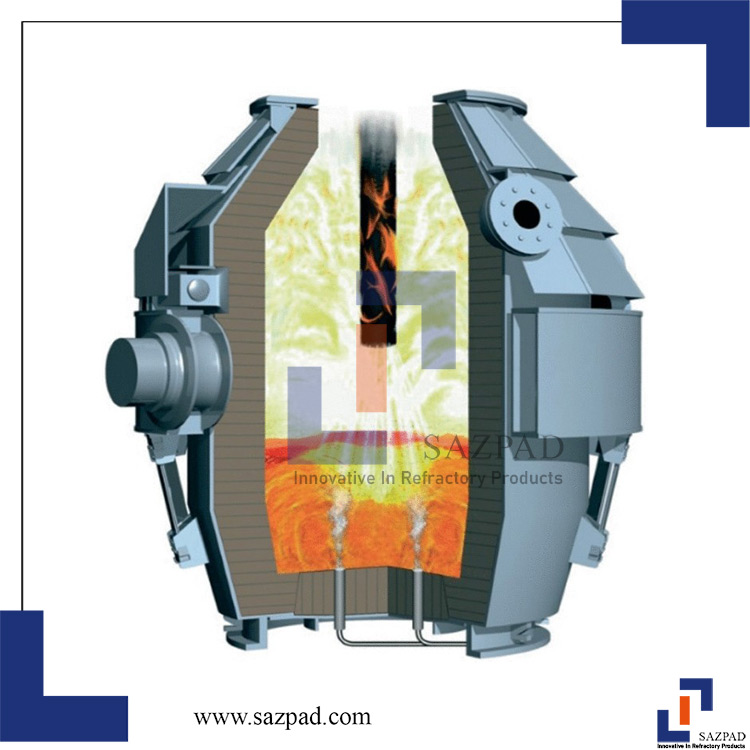
استفاده از جرم نسوز در کف کوره اکسیژن پایه (Hearth of the Basic Oxygen Furnace)
کف کوره BOF یا کنورتور، دقیقا جاییست که مذاب و سرباره در داغترین حد ممکن، در آن حضور دارد. از طرفی دیگر، مذاب و سرباره در کف کوره، به طور مداوم حرکت میکند. تلاطم مذاب، احتمال سایش در این ناحیه را بالا میبرد. کف کوره اکسیژن قلیایی را میتوان، پر تنشترین ناحیه کوره اکسیژن قلیایی دانست. از این رو، کف کنورتور باید بر مبنای تحمل دمای زیاد، تحمل تنشهای مکانیکی شدید و تحمل خوردگی و انحلالهای ناشی از سرباره، ساخته شود. جرم و قطعات نسوز، اگر به درستی و مطابق با نیازهای کف کوره BOF انتخاب شوند، میتوانند در برابر بدترین شرایط حرارتی، مکانیکی و شیمیایی موجود، مقاومت کنند. کف کنورتور یا همان کف کوره اکسیژن پایه، عمدتا با استفاده از جرم یا آجرهای نسوز منیزیایی، جرم یا آجر نسوز دولومیتی، جرم یا آجر نسوز کروم-منیزیا ، جرم یا آجر نسوز منیزیا-کربن و جرم یا آجر نسوز اسپینلی، پوشش داده میشوند. توجه داشته باشید، آجر نسوز یا ماتریس نسوز مورد استفاده در کف BOF، باید از ظرفیت تحمل حرارت 1600 درجه سانتیگراد، بهره ببرد.
پیشنهاد برای مطالعه
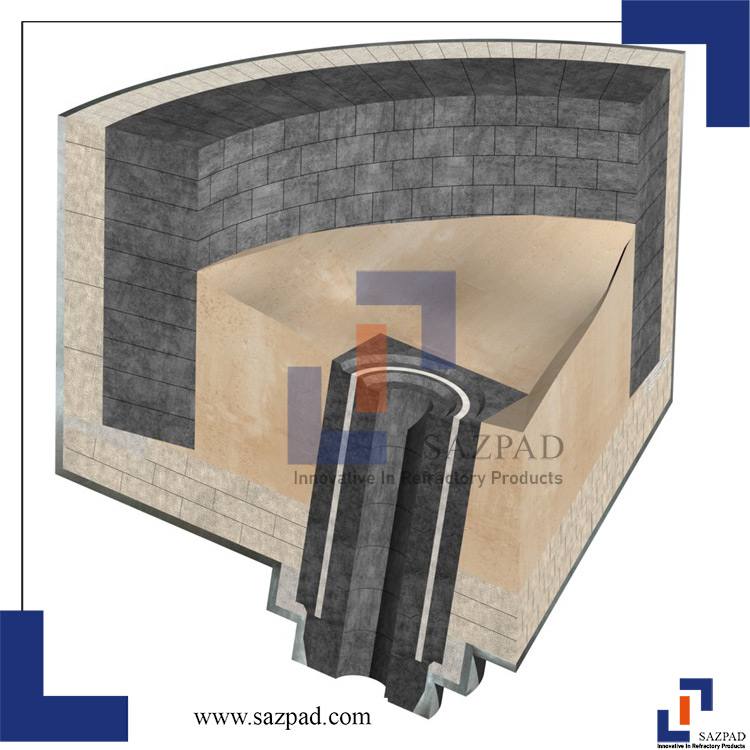
خط خروجی (Tap Hole of the Basic Oxygen Furnace)
نازل خروجی در کوره اکسیژن قلیایی، در واقع مجرایی برای خروج مذاب فولاد از کوره است. در تپ هول یا نازل خروجی کنورتور، حرارت به اندازه دمای فولاد مذاب (1400 الی 1600 درجه سانتیگراد) بالا است. از طرفی جریان مذاب فولاد در حین خروج و فشار مذاب بالا دستی، میتواند منجر به فرسایش تپ هول شود. از این رو، نازل خروجی عمدتا با استفاده از انواع قطعات پیش ساخته دیرگداز و یا جرمهای نسوز مبتنی بر منیزیا، آلومینا و سیلیس، ساخته میشوند.
جرم نسوز در سقف کوره اکسیژن قلیایی (Roof of the Basic Oxygen Furnace)
با توجه به واکنشهای گرمازا هنگام تزریق اکسیژن، حرارت در سقف کوره BOF، به 1600 درجه سانتیگراد نیز میرسد. از طرفی، به دلیل توقف و شروع مجدد عملیات یا تغییر در میزان تزریق اکسیژن، شدت تغییرات ناگهانی حرارت در ناحیه سقف کوره، زیاد است. علاوه بر این، سقف کوره تحت تنشهای مکانیکی قابل توجه ناشی از انبساط و انقباض مواد، ضربات مکانیکی ناشی از بارگذاری و… قرار دارد. همچنین، سقف کوره در معرض گازهای خورنده و ترکیبات شیمیایی قرار دارد. اکسیژن تزریقی، گازهای احتراقی و ترکیبات حاصل از ذوب فلزات میتوانند باعث خوردگی مواد سازنده سقف شوند. سقف کوره اکسیژن قلیایی، به منظور تحمل شرایط موجود، عمدتا از قطعات نسوز پیش ساخته مبتنی بر منیزیا-کروم و یا مبتنی بر منیزیا-کربن، ساخته میشوند.
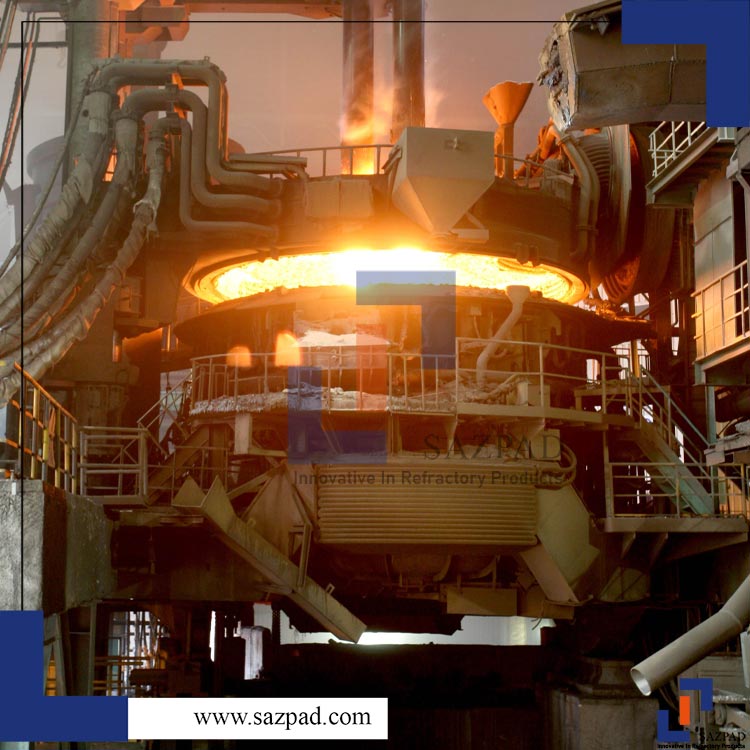
جرم نسوز در لنس کنورتور (Tuyeres of the Basic Oxygen Furnace)
لنس اکسیژن از چند منفذ یا سوراخ که برای دمیدن اکسیژن به داخل کوره اکسیژن قلیایی استفاده میشوند، تشکیل شده است. نواحی اطراف لنس اکسیژن و منافذ دمنده با مواد نسوز پوشانده میشوند تا در برابر حرارت شدید، سایش و خوردگی ناشی از واکنشهای شیمیایی مقاوم باشند.
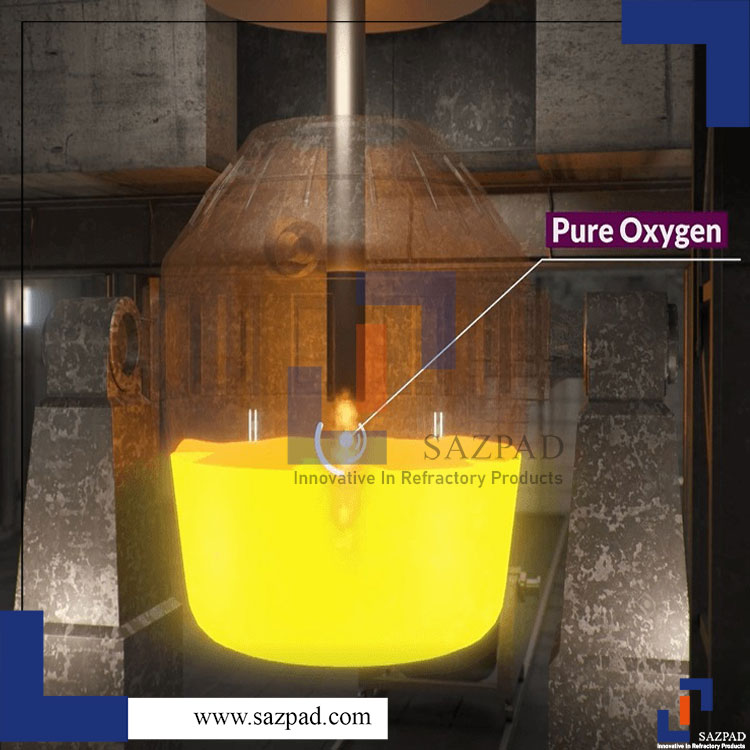
جرم نسوز در ناحیه بارگیری کنورتور (Charging Zone of the Basic Oxygen Furnace)
ناحیه بارگیری در کوره اکسیژن قلیایی، دقیقا جایست که مواد اولیه فولاد سازی یعنی آهن مذاب، ضایعات فولادی، آهک و سایر افزودنیها، از آن ناحیه به داخل کوره BOF، شارژ میشوند. حرارات در این ناحیه از کنورتور، با دمای مذاب آهن یعنی دمای 1600 درجه سانتیگراد، برابر است. توجه داشته باشید، شارژ مواد اولیه در کوره اکسیژن پایه، ضربات شدیدی را به ناحیه بارگیری اعمال میکند. از طرفی وزن قراضه، مذاب آهن و دیگر مواد اولیه بسیار زیاد است، بنابراین فشار مکانیکی زیادی به ناحیه بارگیری وارد میشود. علاوه بر این، ترکیبات ورودی و گازهای موجود، میتواند منجر بر واکنشهای شیمیایی مخرب و در نهایت وقوع خوردگی در ناحیه بارگیری کوره اکسیژن پایه شود. از این رو، ناحیه بارگیری کنورتور، به وسیله جرمهای نسوز، پوشش مییابند. این پوشش نسوز، ناحیه بارگیری کنورتور را به مراتب تقویت میکند. جرم نسوز آلومینایی، جرم نسوز دولومیتی، جرم نسوز زیرکونی به صورت جرمهای نسوز ریختنی و جرمهای نسوز کوبیدنی، در این ناحیه استفاده میشوند.
پیشنهاد برای مطالعه
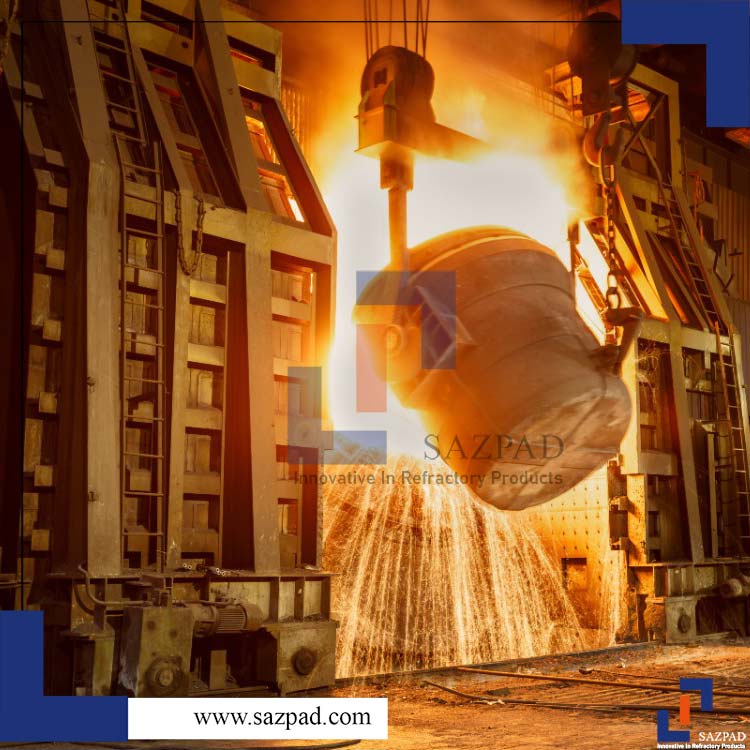
معیارهای انتخاب مخلوط های دیرگداز برای کورههای BOF
در صورت نیاز به انتخاب جرم نسوز در کوره اکسیژن قلیایی، باید حتما به ویژگیهای زیر توجه داشته باشید.
- مقاومت در برابر شوک حرارتی : شوک حرارتی در کورههای اکسیژن قلیایی بسیار زیاد است. توده نسوز در کوره اکسیژن قلیایی باید مقاومت بالایی در برابر شوک حرارتی داشته باشد و با تغییرات دمایی دچار آسیب نگردد.
- مقاومت در برابر خوردگی : با توجه به تاثیرات فرآیندهای شیمیایی در ماتریسهای نسوز، پیشنهاد میشود که جرم نسوز در کوره اکسیژن قلیایی مقاومت بالایی در برابر خوردگی داشته باشد.
- مقاومت در برابر رطوبت: توده نسوز در کوره اکسیژن قلیایی باید در برابر رطوبت و عوامل این چنینی مقاوم باشد تا آسیب نبیند. مقاومت مکانیکی بالا: جرم نسوز در کوره اکسیژن قلیایی باید در برابر ضربه و فشارهای وارده مقاومت خوبی از خود نشان دهد و بتواند وزن های بالای فلزات را نیز تحمل کند.
مزایا و محدودیت های استفاده از جرمهای نسوز در کوره BOF
اجرای جرم نسوز در کوره اکسیژن قلیایی میتواند باعث افزایش مقاومت کورهها در برابر شوک حرارتی شود. اگر توده نسوز در ضخامت بهینه در کورههای BOF مورد استفاده قرار گیرد، میتواند در برابر تغییرات دمایی شدید عملکرد بسیار خوبی از خود نشان دهد. علاوه بر این موضوع، اجرای این دسته دیرگدازها، امکان کنترل وضعیت فولاد و خواص مکانیکی آن را برای تولید کنندگان این محصول فراهم میکند.
با وجود مزایای استفاده از ماتریسهای دیرگداز در کوره اکسیژن قلیایی، این جرمهای نسوز دارای محدودیتهایی نیز هستند که توجه به آنها خالی از لطف نیست. در اولین قدم باید توجه داشت که ماتریس نسوز در کوره اکسیژن قلیایی باید حتما با ضخامت مناسب اجرا شود، ولی برخی از جرمهای نسوز به دلیل ماهیتی که دارند باید در ضخامتهای بالا اجرا شوند که این موضوع میتواند محدودیت فضایی ایجاد کند. علاوه بر این موضوع، برخی از جرمهای نسوز، حساسیت بالایی در برابر رطوبت دارند که این موضوع استفاده از آن ها را در کوره با چالش مواجه میکند.
بهینه سازی عملکرد جرمهای دیرگداز در کوره BOF
یکی از مهمترین فرآیندهایی که میتوان برای بهبود عملکرد جرم نسوز در کوره اکسیژن قلیایی انجام داد، بهینه سازی عملکرد این جرمها است. از طریق دو فرآیند میتوان جرمهای دیرگرداز را بهینه سازی کرد. در اولین فرآیند باید ضخامت و همچنین نحوه اجرای ماتریس دیرگداز در کوره اکسیژن قلیایی را مورد بررسی قرار داد و با توجه به نیاز کوره اکسیژن قلیایی یا همان کوره BOF آن را بهینه سازی کرد.
راه حل دیگری که موضوع بسیاری از مطالعات و مقالات است، بهینه سازی عملکرد جرم نسوز در کوره اکسیژن قلیایی با مواد افزودنی است. مواد افزودنی بسیار متنوعی در صنعت تولید این جرمها موجود هستند که میتوانند برای تولید جرمهای دیرگداز و بهبود عملکرد آنها مورد استفاده قرار گیرند. این افزودنیها خواص شیمیایی، حرارتی و مکانیکی جرم نسوز در کوره اکسیژن قلیایی را بهبود میبخشند. با افزایش مقاومت جرمهای نسوز در این کوره ها، طبیعتا میزان دوام و مقاومت کورهها یا دیگر تجهیزات پوشش یافته با جرم نسوز نیز افزایش پیدا میکند.
چگونگی طراحی و مهندسی مواد دیرگداز برای کنورتورهای اکسیژن
کنوتورهای اکسیژن یا کورههای اکسیژن قلیایی با دمیده شدن اکسیژن برای تولید فولاد کار میکنند. اجرای جرم نسوز در کوره اکسیژن قلیایی یکی از مهمترین اقدامات برای کنترل وضعیت فولاد تولیدی در این کورهها است. به طوری که باید حتما کنوتورهای اکسیژن بتوانند بهترین عملکرد را از خود نشان دهند و امکان تولید فولاد را با توجه به نیاز مصرفی، فراهم نمایند. طراحی و مهندسی مخلوط دیرگداز در کوره اکسیژن قلیایی باید با تیم متخصص و باتجربه انجام شود. در ابتدا باید وضعیت کوره اکسیژن قلیایی و همچنین نوع فولاد مورد نیاز برای تولید مشخص گردد و سپس با توجه به آن، مراحل طراحی و مهندسی مواد دیرگداز در کوره اکسیژن قلیایی انجام گیرد.
ملاحظات طراحی پوششهای نسوز در کورههای اکسیژن قلیایی
توجه به ضخامت در هنگام طراحی پوشش نسوز در کوره اکسیژن قلیایی از اهمیت بسیار زیادی برخوردار است. بالا بودن ضخامت مخلوط نسوز در کوره اکسیژن قلیایی باعث میشود تا عملکرد تودههای نسوز بهبود پیدا کند و بتوان کنترل بیشتری در هنگام تولید فولاد در کوره داشت. با این حال ضخامت توده نسوز در کوره اکسیژن قلیایی باید به صورت بهینه انتخاب شود. مهندسین طراح و مجری ماتریسهای نسوز در کوره اکسیژن قلیایی میتوانند با انجام محاسبات تخصصی، بهترین ضخامت را برای توه نسوز در کوره اکسیژن قلیایی تعیین کنند.
علاوه بر این موضوع، طراحی توده دیرگداز یا نسوز در کوره اکسیژن قلیایی باید با توجه به ترکیبات استفاده شده در ماتریس نسوز انجام شود. به طوری که برای افزایش مقاومت کوره های اکسیژن قلیایی در برابر مواد شیمیایی و همچنین خوردگی، از ترکیبات مناسب در پوششهای نسوز که شامل منیزیت، سیلیکا، سیمان و … هستند استفاده شود. همه این موارد نیاز به محاسبات مهندسی دقیق و تخصص و تجربه تولید کنندگان دارد.
نصب و اجرای مخلوطهای نسوز در کوره BOF
برای اجرای توده دیرگداز در کوره اکسیژن قلیایی در اولین قدم باید نوع ماتریس یا مخلوط نسوز از بین خانواده بزرگ محصولات نسوز از جمله توده دیرگداز کوبیدنی، توده دیرگداز پاششی، توده دیرگداز ریختنی، توده دیرگداز شاتکریت، توده دیرگداز پلاستیک و… تعیین شود. چرا که نحوه اجرای هر یک از انواع این جرمهای نسوز با هم متفاوت است. با توجه به دستور العمل سازنده ماتریس نسوز در کوره اکسیژن قلیایی، اجرای آن میتواند متفاوت باشد. اما باید توجه داشت که برای اجرای این مخلوطهای نسوز با هر روشی، باید سطح کوره به طور کامل تمیزکاری شود تا هیچ گونه آلودگی روی سطح باقی نمانده باشد.
سپس میتوان با روش های ذکر شده، جرم نسوز در کوره اکسیژن قلیایی را اجرا و مورد استفاده قرار داد. پس از تمیز کردن سطح، میتوان ماتریس نسوز را ترکیب و آماده سازی کرد. در مرحله بعدی با تجهیزات مناسب مانند تفنگهای پاشش، ماله و هر وسیله دیگری، جرم نسوز در کوره اکسیژن قلیایی اجرا میشود. برای بهره مندی از عملکرد مناسب ماتریس یا مخلوط دیرگداز در کوره اکسیژن قلیایی، حتما باید میزان ضخامت توده نسوز مورد بررسی قرار گیرد. در صورت نیاز به کسب اطلاعات بیشتر در مورد نحوه اجرا، میتوانید از تولید کننده و یا عرضه کننده محصولات نسوز راهنمایی بگیرید. مجموعه سازپاد، به عنوان یکی از معتبرترین عرضه کنندگان محصولات نسوز، آماده پاسخگویی به سوالات شما است. برای ارتباط با مشاوران فروش محصولات نسوز سازپاد، میتوانید از طریق راههای ارتباطی مندرج در وب سایت سازپاد، اقدام نمایید.
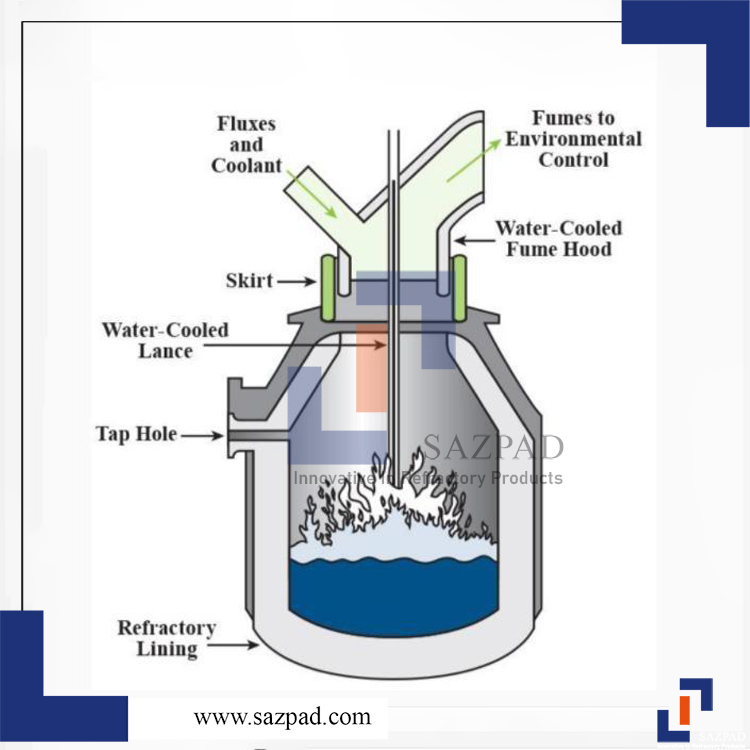
تجهیزات مورد نیاز در نصب تودههای نسوز در کوره های BOF
با توجه به اینکه جرم نسوز در کوره اکسیژن قلیایی با روشهای مختلفی از قبیل پاششی، ریختنی و کوبیدنی اجرا میشوند، تجهیزات مختلفی نیز بر اساس نحوه اجرا مورد نیاز هستند. تجهیزات ایمنی باید در هر یک از روشهای اجرای مخلوطهای نسوز در کوره اکسیژن قلیایی استفاده شوند که شامل ماسک، دستکش و فراهم کردن سیستم تهویه هوا است. علاوه بر این وسایل، تجهیزات دیگری مانند میکسرها جهت مخلوط کردن ماتریس نسوز، تفنگهای پاششی برای اجرای جرم پاششی، ماله برای اجرای جرم ریختنی و پوششی و چکشهای دستی یا چکشهای پنوماتیک برای اجرای جرم نسوز کوبیدنی، مورد نیاز خواهد بود.
پیشنهاد برای مطالعه
استفاده از نانوتکنولوژی در مخلوطهای نسوز برای افزایش عملکرد کورههایBOF
فناوری نانو میتواند برای بهینه سازی توده نسوز در کوره اکسیژن قلیایی مورد استفاده قرار گیرد. فاز نسوز کم کربن در کوره اکسیژن قلیایی باعث افزایش مقاومت این کورهها در برابر دمای بالا میشود و میتواند عملکرد جرم دیرگداز را در برابر شوک حرارتی افزایش دهد. با استفاده از نانو تکنولوژی در ماتریس نسوز در کوره اکسیژن قلیایی، میتوان مقاومت این دیرگدازها را در برابر فرسایش چندین برابر کرد.
عملکرد نانو تکنولوژی در جرم نسوز در کوره اکسیژن قلیایی به قدری مهم است که میتواند از ترک خوردگی و پوسته پوسته شدن مخلوطهای دیرگداز جلوگیری کند. علاوه بر این، چقرمگی ماده افزایش پیدا خواهد کرد. برای افزایش مقاومت ماتریس نسوز در برابر اکسیداسیون و سایر فرآیند فرسایشی نانوتکنولوژی بسیار عالی عمل میکند.
تعمیر و نگهداری کنورتورها و نقش مخلوطهای نسوز در تعمیر انها
ماتریس نسوز در کوره اکسیژن قلیایی میتواند از ترک خوردگی و آسیب دیدگی دیواره بیرونی این کورهها جلوگیری کند. مخلوط های نسوز میتوانند تعمیر و نگهداری از مخلوطهای نسوز را سادهتر کنند و در عین حال باعث بهبود عملکرد جرم های نسوز شوند. از این رو برای کاهش نیاز به تعمیرات و نگهداری، میتوان از جرم نسوز در کوره اکسیژن قلیایی استفاده کرد. البته باید توجه داشت که خود جرمهای نسوز نیاز به مراقبت، دقت و توجه بسیار زیادی دارند. باید به صورت دورهای سطح جرم نسوز در کوره اکسیژن قلیایی مورد بررسی قرار گیرد که دچار ترک خوردگی و آسیب نگردد. در صورت آسیب دیدگی توده دیرگداز یا نسوز در کوره اکسیژن قلیایی، حتما باید مراحل تعمیر آن به درستی انجام شود.
قیمت جرم نسوز مصرفی در کورههای اکسیژن قلیایی چگونه تعیین میشود؟
قیمت جرم نسوز در کوره اکسیژن قلیایی وابسته به نوع مخلوط نسوز و ویژگیهای آن است. انواع مخلوط نسوز در کوره اکسیژن قلیایی میتوانند با مواد اولیه متفاوت تولید شوند. این مواد اولیه متفاوت، میتوانند قیمت جرم نسوز در کوره اکسیژن قلیایی را تغییر دهند. به طور کلی، برخی از مواد اولیه مانند آلومینا قیمت ارزانتری نسبت به سیلیکا، منیزیا و … دارد. همین موضوع باعث شده تا قیمت مخلوط دیرگداز یا نسوز در کوره اکسیژن قلیایی بر اساس مواد اولیه محاسبه و تعیین شود. علاوه بر اینکه قیمت ماتریس نسوز در کوره اکسیژن قلیایی بر اساس مواد اولیه مشخص می گردد، لازم است که این ماتریسهای نسوز با اکیپهای اجرایی متخصص نیز اجرا گردند. از این رو، دستمزد اجرای ماتریس نسوز در کوره اکسیژن قلیایی نیز میتواند روی قیمت نهایی آن موثر باشد. توجه کنید که ضخامت توده نسوز در کوره اکسیژن قلیایی، میزان مواد اولیه مورد نیاز برای اجرای ماتریس نسوز را مشخص میکند و طبیعتا هر چقدر ضخامت بیشتر باشد، شاهد افزایش قیمت اجرای جرم نسوز در کوره اکسیژن قلیایی خواهیم بود. در هر حال، برای استعلام قیمت روز انواع جرم و محصولات نسوز و همچنین دریافت مشاوره برای بهترین انتخاب جرم نسوز، میتوانید با کارشناسان ما در مجموعه سازپاد، ارتباط بگیرید. برای برقراری ارتباط با کارشناسان فروش و مشاوران محصولات نسوز سازپاد، میتوانید به صفحه تماس با ما وب سایت سازپاد، مراجعه نمایید.
راهبردهای بهینه سازی هزینه در تهیه جرمهای نسوز برای کورههای اکسیژن قلیایی
با توجه به شرایط خشن حاکم بر کوره اکسیژن قلیایی، صدمه زیادی به دیواره ها و ساختار اصی کوره BOF وارد میشود. مخصوصا اگر ساختار کوره به پوشش نسوز، مجهز نشده باشد. در هر حال، ادامه حیات کوره، به تعویض و تعمیر صدمههای ایجاد شده در کوره اکسیژن قلیایی، نیاز خواهد داشت. بهینه سازی هزینههای تعمیرات و نگهداری کورههای اکسیژن قلیایی با کمک بکارگیری مخلوطهای نسوز در کوره اکسیژن قلیایی قابل انجام است. میتوان با توجه به حداقل ضخامت توده دیرگداز در کوره اکسیژن قلیایی، این ماتریس نسوز را اجرا کرد و هزینهها را نیز بهینه سازی نمود. اجرای جرم نسوز در کوره اکسیژن قلیایی، میتواند تاثیر مثبتی روی کاهش هزینه ها داشته باشد.