صنعت آهن و فولاد، به عنوان یکی از زیرساختهای حیاتی تولیدات جهانی، نقش بسیار اساسی در توسعه و پیشرفت مختلف حوزههای زندگی انسانی ایفا میکند. پیشرفت در تکنولوژی ساخت تجهیزات مورد استفاده در صنعت آهن و فولاد، علاوه بر صرفه اقتصادی و زمانی برای کارخانهها، کیفیت محصولات نهایی را نیز افزیش میدهد و روی عملکرد هرچه بهتر تجهیزات، مستقیما اثرگذار است. صنعت فولاد از مقادیر قابل توجهی از مواد خام (عمدتا سنگ آهن، ذغال سنگ و ضایعات آهنی) و انرژی استفاده میکند. همچنین یک منبع عمده تولیدکننده پسماندهای محیط زیستی مانند گرد و غبار، فلزات سنگین، دیاکسید گوگرد و… میباشد.
در تولید فولاد، کورههای بلند، مبدلها، پاتیل، تاندیشها و دیگر تجهیزات صنعت آهن و فولاد با دماها و فشارهای بسیار بالا مواجه هستند. این تجهیزات نه تنها با چالشهای حرارتی، بلکه با نیروهای خورنده نیز مواجه هستند. از طرف دیگر، این تجهیزات ناچار به مقابله با احتمال سایش و ضربه در طول فرآیند تولید هستند. پس، به منظور افزایش عمر مفید این تجهیزات و افزایش بهرهوری، استفاده از مواد نسوز با ویژگیهای مناسب در ساختار آنها بسیار اساسی به نظر میرسد. در ادامه، انواع قطعات و جرمهای نسوز مورد استفاده در صنعت آهن و فولاد و همچنین کاربرد جرم و قطعات نسوز در این صنعت و مزایا و معایب استفاده از آن، مورد بحث و بررسی قرار گرفته است.
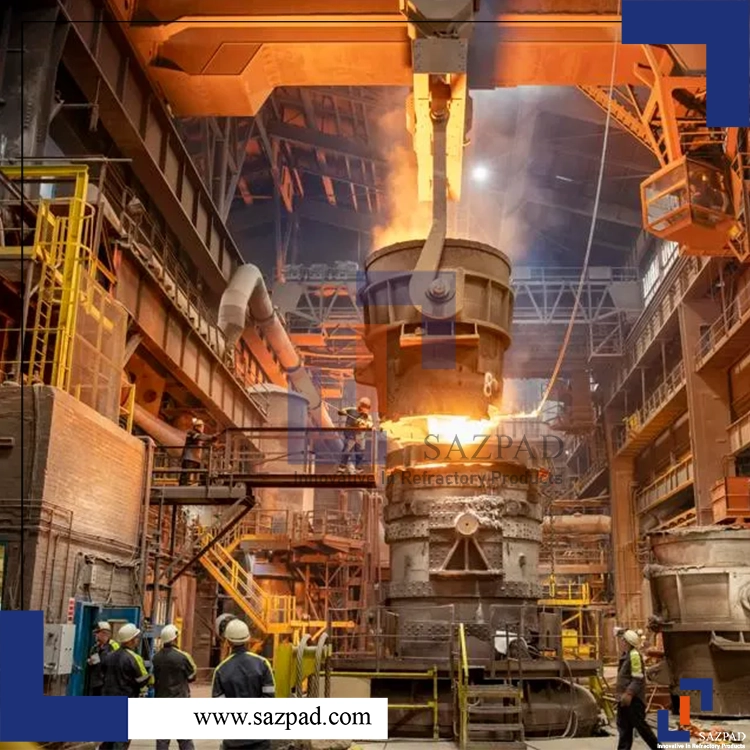
جرم نسوز (جرم دیرگداز) چیست؟
جرم نسوز یا Refractory Mass یکی از مواد کاربردی در صنایع مختلف است. جرم نسوز که با نام جرم یا توده دیرگداز هم شناخته میشود به موادی گفته میشود که در مقابل حرارت بالا مقاوم است. همچنین کلیه خواص فیزیکی، شیمیایی، مکانیکی و ترمودینامیک این مواد نسوز، در برابر حرارت بالا،تغییر نمیکند و در برابر سایش، خوردگی شیمیایی، فشار و شوک حرارتی بسیار مقاوم است. ویژگی و مزایای انواع جرمهای نسوز، موجب شده تا امروزه استفاده از آن در صنایع مختلف، از اهمیت بسیار بالایی برخوردار باشد. این دیرگدازها عمدتاً از سیلیس (SiO2) آلومینا (Al2O3) منیزیم (MgO) و زیرکونیا (ZrO2) تشکیل شدهاند.
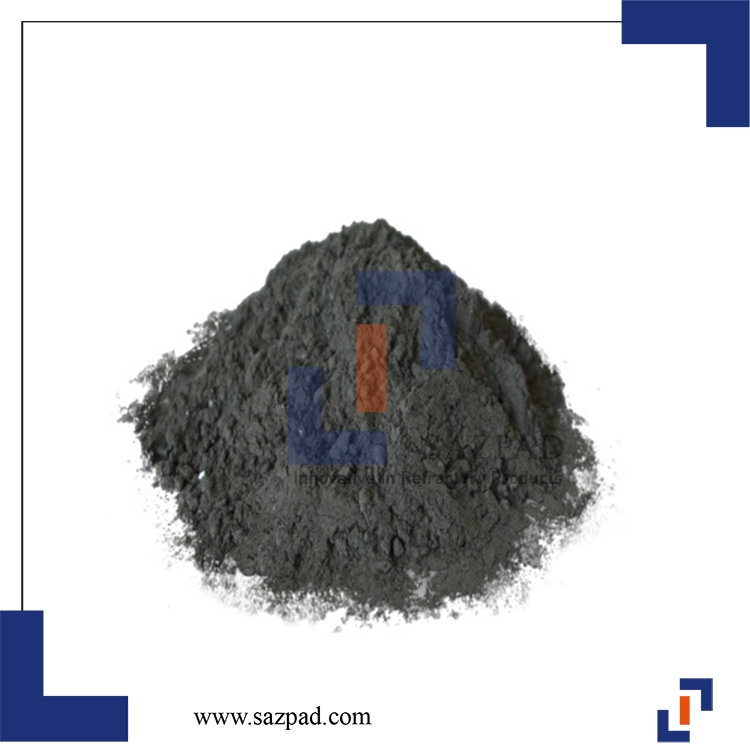
جرم نسوز در صنعت آهن و فولاد چه کاربردی دارد؟
مواد نسوز در صنایع گاز، سیمان، پتروشیمی، نفت، صنایع غذایی و هر صنعت که با حرارتهای بالا سروکار دارند کاربرد دارد. اما در ایران بیشترین استفاده از مواد یا جرمهای نسوز در صنایع فولاد میباشد. صنعت آهن و فولاد، 60 الی 70 درصد از جرم و مواد دیرگداز تولیدی را مصرف میکند، بنابراین توسعه صنعت آهن و فولائ، برای توسعه صنعت مواد نسوز بسیار مهم است. به طور کلی، جرمهای نسوز در تجهیزات مختلف صنعت آهن و فولاد به عنوان پوشش حفاظتی استفاده میشوند و نقش مهمی در کیفیت و خلوص نهایی فولاد تولید شده دارند. در واقع، جرم نسوز یک لایهی محافظ برای تجهیزات در معرض حرارت است که در صنایع مختلفی مانند فولادسازی، پتروشیمی، و کوره آهک کاربرد دارد. این لایه محافظ شرایط و امکان تولید محصولات در صنایعی که حرارت بخش اساسی آنها است را فراهم میکند. اهداف مورد انتظار از هر مواد یا جرم دیرگدازی از نقطه نظر تولیدی به شرح زیر است :
- عدم تاثیر مخرب بر روی تجهیزات
- انطباق با عمر موردنظر تجهیزات
- انطباق با نرخ فرسایش موردنظر
پیشنهاد برای مطالعه
اهمیت مواد نسوز در صنعت آهن و فولاد
این، مقاومت حرارتی، مکانیکی و شیمیایی در انواع جرمهای نسوز است که سبب شده تا این نسوزها در صنایع فولادسازی و تولید آهن به طور گسترده به کار گرفته شوند.. درواقع، جرمهای نسوز با تکیه بر ویژگیهای منحصر به فردشان، از تخریب تجهیزات در معرض حرارت بالا جلوگیری کرده و کیفیت فرآیندهای ذوب برای تولید آهن مذاب را بهبود میبخشند. جرم و قطعات نسور، به عنوان پوششهای حفاظتی تجهیزات در معرض حرارت، عمل کرده و مقاومت بالایی در برابر دمای بالا و مواد خورنده، ارائه میدهد. استفاده از جرمهای نسوز، باعث کاهش تشکیل سرباره و بهینهسازی مصرف انرژی میشود. در نتیجه به کارگیری مواد نسوز در صنعت آهن و فولاد، هزینههای تولید را کاهش و کارایی فرآیند را افزایش میدهد. این امر، همچنین به کاهش آلودگی محیط زیست نیز کمک میکند.
مواد نسوز؛ از ابتدا تا انتهای فرآیندهای صنعت فولاد
مواد نسوز نقش بسیار مهمی در صنعت آهن و فولاد ایفا میکنند. از ابتدا تا انتهای فرآیندهای تولید فولاد، این جرمهای نسوز هستند که برای مقابله با دماهای بالا و شرایط سخت استفاده میشوند. در مرحله ابتدایی، مواد نسوز در کورههای بلند برای تولید آهن از سنگ آهن استفاده میشوند. این کورهها نیاز به آجرهای نسوز با مقاومت حرارتی بالا دارند. پس از تولید آهن خام، این مواد به کورههای قوس الکتریکی منتقل میشوند، جایی که جرمهای نسوز از جنس منیزیت یا کرومیت برای پوشش داخلی استفاده میشوند. در مرحله بعد، در فرآیند پالایش و ریختهگری، آجرهای نسوز و یا جرمهای نسوز آلومینا و زیرکونیا برای پوشش پاتیلها و تاندیشها به کار میروند. هر مرحله از تولید فولاد نیازمند مواد نسوز خاص خود است تا از کارایی و کیفیت نهایی محصول اطمینان حاصل شود. بیایید مراحل مختلف فرآیند تولید فولاد و انواع مواد نسوز مورد استفاده در هر مرحله را بررسی کنیم:
مرحله اول : آهن سازی
کوره بلند : در فرآیند آهنسازی، سنگ آهنوارد کوره بلند شده و طی واکنشهای شیمیایی به آهن مذاب تبدیل میشود. در طی این فرآیندها، دما در کوره بلند به بیش از 1500 درجه سانتی گراد نیز میرسد. به علاوه به علت وجود گازهای خنک کننده، نسوزهای مورد استفاده باید در برابر اکسیداسیون نیز مقاوم باشند. جرمهای نسوز بهکار رفته در آستر کوره بلند، برای مقاومت در برابر دماهای بسیار بالا و نیز واکنشهای شیمیایی شدید طراحی شدهاند. نسوزهای رایج مورد استفاده در کوره بلند شامل آجرهای نسوز یا جرمهای نسوز آلومینوسیلیکات (خاک رس آتش)، نسوزهایی با درصد آلومینای بالا و نسوزهایسیلیسی میباشند. این جرمهای نسوز بدون شکل (مونولیتیک) یا شکل دار با ایجاد یک لایه محافظ در برابر دماهای بسیار بالا و نیز مقاومت در برابر سایش و خوردگی شیمیایی، عمر مفید کوره را افزایش میدهند. علاوه بر این، استفاده از مواد نسوز مناسب باعث بهبود بهرهوری انرژی و کاهش هزینههای نگهداری میشود.
پیشنهاد برای مطالعه
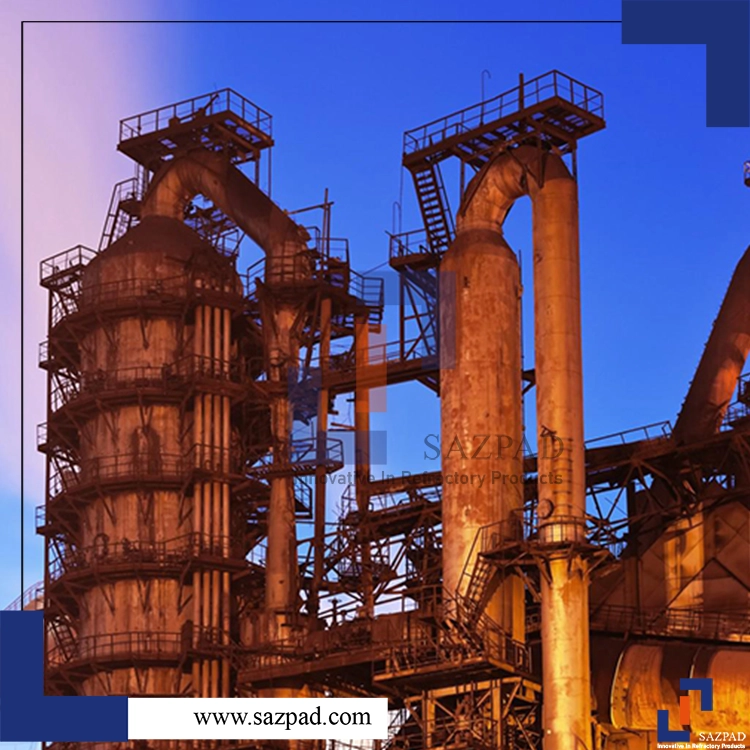
مرحله دوم : فولاد سازی
کوره اکسیژن قلیایی (Basic Oxygen Furnace) : کوره BOF از اساسیترین تجهیزات مرحله دوم یعنی تولید فولاد است. در کوره اکسیژن قلیایی (BOF)، کوره با آهن مذاب تولید شده در مرحله اول و ضایعات فولادی شارژ میشود. پس از آن، اکسیژن خالص با فشار بالا از طریق یک لانس به داخل کوره دمیده میشود. در واقع، اکسیژن دمیده شده با کربن و سایر ناخالصیهای موجود در مذاب آهن واکنش شیمیایی داده و اکسیدهایی مانند CO و CO2 را حاصل میشود. این واکنشهای اکسیداسیونی، دمای داخلی کوره را به بیش از 1600 درجه سانتیگراد افزایش میدهد. این حرارت و دمای بالای ناشی از واکنشهای گرمازا در کورههای اکسیژن قلیایی، برای ذوب و تصفیه آهن مذاب کافی است. پس به همین دلیل، کورههای BOF به تجهیزات گرمایشی خارجی نیاز ندارند و از گرمای تولید شده توسط واکنشهای شیمیایی برای حفظ دمای بالا در کوره استفاده میکنند.در طی این واکنشهای شیمیایی و اکسیداسیونها، کربن و ناخالصیهایی نظیر سیلیسیم، منگنز، فسفر و گوگرد به اکسیدهای خود تبدیل شده و به سرباره منتقل میشوند. سرباره که شامل این اکسیدها و مواد افزودنی مانند آهک است، به سطح آهن مذاب میآید و به طور دورهای تخلیه میشود. در نهایت، ترکیب شیمیایی فولاد به دقت کنترل و تنظیم میشود و در صورت نیاز، عناصر آلیاژی نیز اضافه میگردد. با اتمام فرآیند، فولاد مذاب به قالبهای ریختهگری منتقل و سرد میشود تا به شکل شمش یا دیگر اشکال اولیه فولاد تبدیل شود. کوره اکسیژن قلیایی (Basic Oxygen Furnace)، از اجزای مختلفی تشکیل میشود. در میان این اجزا، میتوان مواد نسوز را اساسیترین جزء در کورههای BOF، نامید. مواد نسوز با ایجاد پوششهای نسوز و محافظ در نواحی مختلف کورههای BOF، پایداری و عملکرد آن را در شرایط خشن فرآیند فولاد سازی تضمین میکند. برای بهینهسازی عملکرد کورههای اکسیژن قلیایی (BOF)، انتخاب صحیح جرمهای نسوز بسیار حائز اهمیت است. جرمهای نسوز مورد استفاده در BOF، باید در برابر حرارت، حملات شیمیایی، سیکل یا شوکهای حرارتی، ضربات و فرسایشهای ناشی از شارژ قراضه و… مقاوم باشند. استفاده از روشهای تحلیل پیشرفته مانند آنالیز TMC نقش بسزایی در بهینهسازی انتخاب جرم نسوز دارد. در واقع آنالیز TMC در انتخاب نسوز مناسب کوره اکسیژن قلیایی، به شناسایی ترکیبات و مواد نسوز مناسبتر برای افزایش عمر مفید و بازدهی کورهها کمک میکنند. در کوره اکسیژن قلیایی، عمدتا از آجر نسوز و جرمهای نسوز مونولیتیک منیزیایی استفاده میشود. چرا که جرم نسوز منیزیایی با نیازهای حرارتی، مکانیکی و شیمیایی کورههای اکسیژن قلیایی، مطابقت دارد.
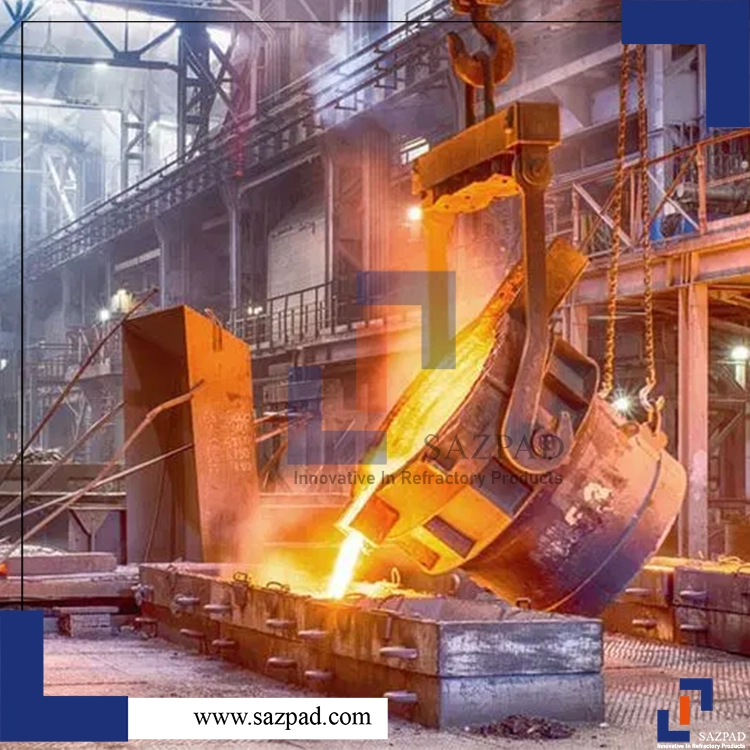
کوره قوس الکتریکی (Electric Arc Furnace) : یکی دیگر از تجهیزات مهم فولادسازی که از انواع جرم و مواد نسوز بهره میبرد، کوره قوس الکتریکی (EAF) است. کوره قوس الکتریکی (Electric Arc Furnace) ، به منظور ذوب ضایعات فولاد بازیافتی و تولید فولاد با کیفیت از ضایعات فولاد، مورد استفاده قرار میگیرد. در واقع، کوره قوس الکتریکی (EAF)با ایجاد قوس الکتریکی بین الکترودهای گرافیتی، دما و حرارتی تقریبا 3000 درجه سانتیگراد را فراهم میکند که این حرارت بالا، منجر به ذوب سریع قراضههای فولاد، مواد آلیاژی و دیگر مواد موجود در کوره میگردد. در طی فرآیند ذوب، با دمش اکسیژن از سطح بالای کوره، ناخالصیهای موجود در مذاب قراضه آهن، اکسید شده و به صورت سرباره به سطح مذاب میآیند و سپس تخلیه میشوند. در نهایت، با رسیدن به مذاب فولاد مورد انتظار، مذاب فولاد به قالبهای ریختهگری منتقل و پس از سرد شدن، در اشکال و ابعاد متنوع برای کاربردهای مختلف آماده میشود. توجه داشته باشید که کورههای قوس الکتریکی مورد استفاده در تولید فولاد باید تحمل این دمای بالا و همچنین آسیبهای ناشی از تلاطم مذاب به دلیل دمش اکسیژن را داشته باشند. ظرفیت تحمل حرارت بالا، حملات شمیایی و تنشهای مکانیکی در کورههای EAF، تنها با استفاده از پوششهای حافظتی از جنس جرمهای نسوز شکل دار و یا جرمهای نسوز بدون شکل (مونولیتیک)، تامین میشود. در شرایط حرارتی، مکانیکی و شیمیایی سخت کورههای قوس الکتریکی، عمدتا از جرمهای نسوز کوبیدنی، جرمهای نسوز ریختنی، جرمهای نسوز پلاستیک و آجرهای نسوز پایه منیزیایی و آلومینایی استفاده میشود.
پیشنهاد برای مطالعه
مرحله سوم : ریختهگری و شکل دهی
در گام ریختهگری و شکلدهی، فولاد مذاب، به طور مرحله به مرحله، به وسیله پاتیل حمل مذاب (بوتهها) و مخازن نسوز، از کورههای اکسیژن قلیایی و کورههای قوس الکتریکی به وسیله ماشینهای ریخته گری به تاندیشها یا کانالهای ریختهگری هدایت میشود. تاندیشها با کنترل جریان، مذاب فولاد را به قالبهای ریختهگری منتقل میکنند. تمامی تجهیزات گام ریختهگری و شکل دهی مذاب فولاد، اعم از پاتیلهای حمل مذاب فولاد، مخازن نگهداری مذاب، ماشینهای ریختهگری، کانالهای ریختهگری (تاندیش) و قالبها، همگی باید توانایی عملکرد در شرایط حرارتی و دمای بالا، واکنشهای شمیایی و تنشهای مکانیکی را داشته باشند. بدین منظور، به طور گسترده از انواع مختلف جرمها و قطعات نسوز در بخشهای مختلف تجهیزات ریختهگری و شکل دهی، استفاده میشود. از رایجترین جرم و قطعات نسوز مورد استفاده در تجهیزات ریختهگری و شکل دهی فولاد مذاب، میتوان به آجرهای نسوز آلومینایی، آجرهای نسوز منیزیا کربنی، قطعات نسوز پیش ساخته و انواع جرمهای نسوز ریختنی مبتنی بر آندالوزیت، مولایت، آلومینا گرافیت، منیزیم و… اشاره نمود.
مرحله چهارم : عملیات حرارتی
مرحله چهار از تولید فولاد، یعنی عملیات حرارتی، با هدف بهبود و ارتقای ویژگیهای مکانیکی و فیزیکی فولاد، اجرا میشود. فولاد بهصورت جامد و با دمایی پایینتر از نقطه ذوب به سمت تجهیزات عملیات حرارتی هدایت میشود. عملیات حرارتی شامل فرآیندهای آنیلینگ، نرمالسازی، تمپرینگ و کوئنچینگ است. با توجه به شرایط این مرحله از تولید فولاد، بکارگیری جرمهای نسوز در انواع تجهیزات عملیات حرارتی، همچنان مشاهده میشود. در ادامه، هر یک از عملیاتهای حرارتی و نقش مواد نسوز در هر یک از آنها مورد بررسی قرار گرفته است.
- عملیات حرارتی آنیلینگ : در آنیلینگ، فولاد به کورههای آنیلینگ منتقل شده و به آرامی تا دمای بالاتر از دمای نقطه بحرانی (دمای 700 الی 900 درجه سانتیگراد) گرم شده و سپس در کوره یا در یک محیط کنترلشده بهتدریج خنک میشود. با آنیلینگ فولاد، تنشهای داخلی آن کاهش و انعطافپذیری فولاد به مراتب بهبود مییابد. در عملیات آنیلینگ، انواع قطعات و جرمهای نسوز در دیوارها و کف کورههای آنیلینگ، به منظور تحمل دما، ایجاد عایق و حفظ گرمای کوره آنیلینگ، بکار گرفته میشوند.. استفاده از آجرهای نسوز آلومینایی، آجرهای نسوز سیلیسی و آجرهای نسوز منیزیایی در کورههای آنیل فولاد متناسب با شرایط دمایی، حرارتی و شیمیایی موجود در کوره آنیلینگ، بسیار رایج است.
- عملیات حرارتی نرمالسازی : در نرمالسازی، فولاد پس از انتقال به کورههای نرمال سازی، تا دمای بالاتر از دمای آنیلینگ، گرم شده و سپس با قرارگیری در معرض هوا، خنک میشود. نرمال سازی فولاد، یکنواختی ساختار و خواص مکانیکی فولاد را افزایش میدهد. در کورههای نرمالسازی فولاد، به منظور ایجاد عایق حرارتی مناسب، توزیع یکنواخت حرارت در داخل کوره، مقاومت کوره در برابر شوکهای حرارتی و حفاظت از تجهیزات کوره در برابر دماهای بالا، از جرمهای نسوز و قطعات نسوز در ساخت کوره نرمال سازی استفاده میشود. جرمهای نسوز، دمای کوره را کنترل و به تعادل دمای داخل کوره، کمک میکنند. استفاده از قطعات جرمهای نسوز در دیوارها و کف کورههای نرمال سازی فولاد، در به دست آوردن ساختار و خواص میکروسکوپی مطلوب فولاد بعد از عملیات نرمالسازی، بی تاثیر نیستند.
- عملیات حرارتی کوئنچینگ : در کوئنچینگ فولاد گرم شدن تا دمای بحرانی (آستنیتی) به سمت کورههای مخصوص گرمایش هدایت میشود. فولاد در عملیات کوئنچینگ، پس از گرم شدن، به تانکهای کوئنچینگ منتقل و در آب، روغن یا هوا به سرعت خنک میشود. با عملیات حرارتی کوئنچینگ فولاد، سختی و استحکام فولاد افزایش مییابد. در کورههای مخصوص گرمایش مجدد فولاد، از انواع آجرهای نسوز مبتنی بر آلومینا، سیلیکا و منیزیا در لاینینگ کف و دیوارهها استفاده میشود. قطعات و جرمهای نسوز در کورههای گرمایش مجدد، به قطعات فولادی کمک میکنند تا قبل از کوئنچینگ، به طور یکنواخت به دمای مورد هدف برسند. در واقع، این جرمهای نسوز هستند که به طور موثر از خطرات مرتبط با تغییرات دما، واکنشهای شیمیایی، و تنشهای مکانیکی در کورههای گرمایش مجدد، جلوگیری میکنند.
- عملیات حرارتی تمپرینگ : تمپرینگ فولاد که با هدف افزایش مقاومت در برابر خستگی و کنترل سختی فولاد انجام میشود، فولاد کوئنچ شده به کورههای تمپرینگ منتقل و تا دمایی زیر دمای بحرانی (دمای150 الی 650 درجه سانتیگراد) گرم میشود و سپس به آرامی خنک میشود. در عملیات تمپر کردن فولاد، جرم و مواد نسوز، نقش بسزایی در تجهیزات مورد استفاده برای گرمایش و نگهداری فولاد در دماهای خاص دارند. کورههای تمپرینگ، عمدتا با انواع جرمهای نسوز، لاینینگ میشوند. پوششهای نسوز، عایق حرارتی را در کورههای تمپرینگ تامین میکنند. به علاوه از پوسته کوره و دیگر تجهیزات اساسی آن، در برابر حرارت بالای ایجاد شده در طول فرآیند تمپر، محافظت میکنند. استفاده از مواد نسوز در کورههای تمپرینگ، گرما را به طور یکنواخت در سراسر محفظه کوره توزیع میکند. این میتواند در تلطیف یکنواخت فولاد، بسیار موثر باشد. به علاوه، تامین گرمایش یکنواخت کوره تمپرینگ توسط پوششهای نسوز تعبیه شده در کوره تمپرینگ، از گرمای بیش از حد موضعی یا گرمای کم که منجر به خواص مکانیکی ناسازگار با هدف تمپرینگ فولاد میشود، جلوگیری میکند. به طور کلی میتوان گفت، مواد نسوز به پایداری حرارتی محیط کوره تمپرینگ کمک میکند و امکان کنترل دقیق دمای حرارت و زمان نگهداری را فراهم میکنند. این برای رسیدن به خواص مکانیکی خاص مورد نیاز فولاد، بسیار مهم است. از رایجترین محصولات نسوز در کورههای تمپرینگ، میتوان به انواع آجرهای نسوز آلومینایی، آجرهای نسوز منیزیایی و آجرهای نسوز سلیکایی اشاره نمود.
پیشنهاد برای مطالعه
نکته !! توجه به این نکته مهم است که مواد نسوز خاص مورد استفاده در هر مرحله ممکن است بسته به عواملی مانند نوع فولاد تولیدی، نوع سرباره و پارامترهای فرآیند و ویژگیهای عملکرد مورد نظر متفاوت باشد. معمولاً از مواد یا جرمهای نسوز مذکور استفاده میشود، اما ترکیبات و محصولات نسوز بسیاری برای کاربردهای مختلف در صنعت فولاد موجود است.
مهمترین خواص مواد نسوز در صنعت آهن و فولاد
خواص یک دیرگداز متاثر از چند عامل مهم میباشد که کنترل هر یک از آنها دارای اهمیت است. مهمترین این عوامل عبارتاند از:
- ریزساختار
- نوع و خلوص مواد اولیه
- تکنولوژی ساخت
- عوامل و شرایط محیطی
یکی از معیارهای مهم مواد و جرمهای نسوز، ظرفیت تحمل حرارتی آنها در مواجه با دمای نسبتا بالا است، به صورتی که جرم نسوز در حین عملیات تغییر شکل ندهد. این مسئله نشاندهنده آن است که جرمهای نسوز باید در دماهای مختلف از نظر فیزیکی و شیمیایی پایدار باشند. این معیار اغلب به وسیله مخروطهای زیگر که خود از مواد سرامیکی هستند، اندازه گرفته میشود. وقتی که ماده نسوز در دماهای مختلف قرار میگیرد، این مخروط ها به خاطر دما نشست میکنند (مقدار نشست به ترکیبات مخروط بستگی دارد) پس از این که حرارت دهی تمام شد ماده نسوز با مخروط زیگر مقایسه میشود و به این صورت مقدار نسوز بودن این ماده اندازه گرفته میشود. از طرف دیگر، واکنشهای شیمیایی و تنشهای مکانیکی نیز میتوانند خواص حرارتی و عملکرد جرمهای نسوز را تحت تاثیر قرار دهند. پس بدین منظور، خاصیت حرارتی، شیمیایی و مکانیکی جرمهای نسوز را میتوان از مهمترین خواص مواد نسوز در صنعت آهن و فولاد و دیگر صنایع دانست. از این جهت، قبل از تهیه هر گونه جرم نسوز، باید کاربرد مورد هدف، با استفاده از آنالیز TMC تحلیل شود و بر اساس نتایج آن، بهترین و متناسبترین جرم نسوز انتخاب و استفاده شود. آنالیز TMC در انتخاب نسوز مناسب کاربردهای صنعت آهن و فولاد، میتواند راندمان تولید فولاد و پایداری تجهیزات را به مراتب افزایش دهد.
دسته بندیهای رایج جرم نسوز در صنعت آهن و فولاد
مواد دیرگداز را میتوان بر اساس معیارهای مختلف به دسته بندیهای متعددی تقسیم بندی نمود:
1. دسته بندی جرم نسوز بر اساس ترکیبات تشکیل دهنده
انواع جرمهای نسوز با توجه به ترکیبات تشکیل دهنده آن ها به 6 دسته اساسی تقسیم بندی میشوند. جرمهای نسوز سیمانی، سیلیسی، آلومینایی، منیزیتی، زیرکونیایی و کرومی از متداول ترین انواع جرمهای نسوز هستند. هر کدام از این جرمها دارای ویژگی خاصی میباشند که با توجه به آن در صنایع مختلف مورد استفاده قرار میگیرند. توجه داشته باشید که جرمهای نسوز میتوانند مینرالهای تک ،دو الی چند جزئی از عناصر نسوز ذکر شده باشند.
2. دسته بندی جرم نسوز بر اساس خواص شیمیایی
انواع جرم نسوز را میتوان با توجه به خواص شیمیایی آنها نیز دسته بندی نمود. به طور کلی جرمهای نسوز بر اساس خواص شیمیایی، در سه دسته اسیدی، بازی و خنثی طبقه بندی میشوند. عمدتا انتخاب جرمهای نسوز، بر اساس نوع سرباره موجود و واکنشهای شیمیایی احتمالی در فرآیند، انتخاب میشوند.
پیشنهاد برای مطالعه
3. دسته بندی جرم نسوز بر اساس روش مصرف
جرمهای نسوز را با توجه به نحوه مصرف آنها نیز میتوان به انواع جرمهای نسوز ریختنی، جرمهای نسوز کوبیدنی، جرمهای نسوز پاشیدنی (گانینگ یا پاشش خشک)، جرمهای نسوز شاتکریت (پاشش تر) و جرمهای نسوز پوششی دسته بندی نمود. روش مصرف جرمها با در نظر گرفتن صنایع مورد نظر انتخاب میشود. توجه داشته باشید که ساختار اولیه هر کدام از این جرمهای نسوز نیز با یکدیگر متفاوت است.
تاثیر مواد نسوز در هزینههای صنعت آهن و فولاد
مواد نسوز در صنعت آهن و فولاد نقش مهمی در کاهش هزینهها و افزایش بهرهوری دارند. این مواد عمدتاً در فرآیندهای حرارتی استفاده میشوند و به طور کلی میتوانند تاثیرات زیر را بر هزینهها داشته باشند:
- کاهش خرابی و خرابی تجهیزات : مواد نسوز معمولاً خصوصیات مقاومتی بالایی دارند و میتوانند در برابر حرارت، فشار و سایر شرایط سخت محیطی مقاومت کنند. با استفاده از این جرمهای نسوز، آسیب و خرابی تجهیزات در فرآیندهای حرارتی کاهش مییابد و نیاز به تعمیر و نگهداری کمتری برای تجهیزات احتمالی است.
- افزایش عمر مفید تجهیزات : با استفاده از مواد و جرمهای نسوز، عمر مفید تجهیزات به طور قابل توجهی افزایش مییابد. این امر باعث کاهش هزینههای جانبی مرتبط با جایگزینی و تعمیر تجهیزات میشود.
- بهبود بهرهوری حرارتی : مواد نسوز معمولاً خصوصیات عایق حرارتی خوبی دارند و میتوانند از انتقال حرارت نامطلوب در فرآیندهای حرارتی جلوگیری کنند. این بهبود در بهرهوری حرارتی میتواند منجر به کاهش مصرف انرژی و در نتیجه هزینههای مرتبط با مصرف انرژی شود.
- کاهش ضایعات مواد : مواد نسوز میتوانند از ضایعات مواد در فرآیندهای حرارتی جلوگیری کنند. این در نتیجه میتواند منجر به صرفهجویی در هزینههای مواد و مدیریت بهتر منابع شود.
بنابراین، استفاده از جرمهای نسوز در صنعت آهن و فولاد میتواند به کاهش هزینهها، افزایش بهرهوری و بهبود عملکرد کلی فرآیندها کمک کند. البته، هزینههای مرتبط با خرید و استقرار مواد نسوز نیز باید در محاسبه هزینههای کلی بررسی شوند.
نقش آنالیز TMC در انتخاب مواد نسوز در صنعت آهن و فولاد
آنالیز (Thermal, Mechanical, and Chemical Analysis) TMC ، یک ابزار مهم برای تحلیل شرایط حرارتی، مکانیکی و شیمیایی تجهیزات مختلف صنایع در معرض حرارت از جمله صنعت آهن و فولاد است که به انتخاب جرم و مواد نسوز مناسب و مطابق با نیازهای موجود در کاربرد، کمک میکند. نقش آنالیز TMC در انتخاب جرمهای نسوز در صنعت آهن و فولاد به شرح زیر است :
- بررسی رفتار حرارتی: آنالیز TMC به مهندسان امکان میدهد تا شرایط دمایی و شوکهای حرارتی موجود در کوره و یا دیگر تجهیزات در معرض حرارت را بشناسند و آسیبهای ناشی از آن را تحلیل کنند. نتایج بررسیهای حرارتی، به انتخاب جرمهای نسوز با ظرفیت تحمل دما و شوکهای حرارتی کاربرد هدف را فراهم میکند. در واقع، مهندسین با شناخت خواص حرارتی مواد نسوز مانند ضریب گسترش حرارتی، نقطه ذوب، مقاومت در برابر حرارت و شوکهای حرارتی و تطبیق این دادهها با نتایج آنالیز حرارتی، مکانیکی و شیمیایی، میتوانند با انتخاب مناسبترین نوع جرمهای نسوز، بهترین عملکرد و بالاترین عمر مفید را در تجهیزات در معرض حرارت صنایع مختلف، فراهم کنند.
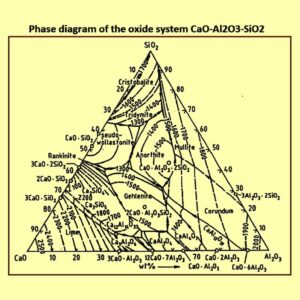
- بررسی رفتار مکانیکی: با آنالیز TMC ، احتمالات ضربه، فرسایش و دیگر آسیبهای ناشی از تلاطم مذاب، نفوذ مذاب، برخورد اجزای سنگین و… در انواع تجهیزات صنعتی، تحلیل میشود. نتایج این تحلیل مکانیکی، دادههای با اهمیت بالا برای انتخاب کارآمدترین نسوز که بتواند شرایط خشن مکانیکی موجود در تجهیزات صنعتی را تحمل کند، بدست میآید. این دادهها، خصوصیات مکانیکی مورد انتظار از تودههای نسوز مانند مقاومت به کشش، مقاومت به فشار، مدول الاستیسیته، مقاومت به خستگی حرارتی، انعطافپذیری و… را تعین میکنند.
- بررسی رفتار شیمیایی: آنالیز TMC یا همان تحلیل حرارتی، مکانیکی و شیمیایی، همانطور که از اسمش مشخص است به علاوه سنجش شرایط حرارتی و مکانیکی تجهیزات صنعتی، شرایط شیمیایی موجود در آنها را نیز ارزیابی میکند. دادههای حاصل از بررسی شیمیایی، مهندسین را در جریان شرایط و واکنشهای شیمیایی در حین عملیاتهای مختلف تجهیزات صنعتی قرار میدهد. این اطلاعات امکان تطبیق جرمهای نسوز مناسب و متناسب با شرایط شیمیایی موجود در کاربردهای خاص را فراهم میسازد. با استفاده از دادههای به دست آمده از آنالیز TMC و با درک ویژگیهای شیمیایی جرمهای نسوز، مهندسین میتوانند بسته به شرایط فعلی، بهترین جرمهای نسوز را انتخاب کرده و عملکرد پایدار تجهیزات صنعتی را در مقابل شرایط شیمیایی دشوار تضمین نمایند.
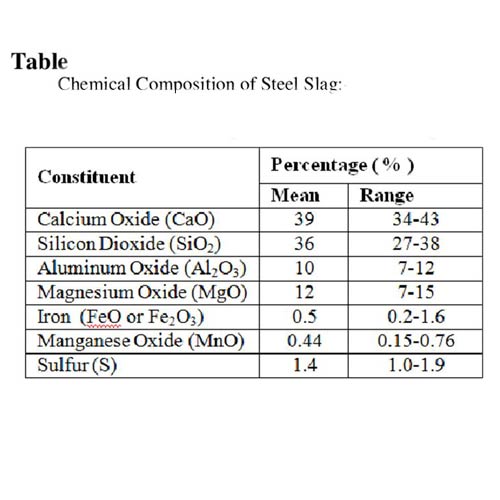
خلاصه!! با استفاده از آنالیزTMC، مهندسان میتوانند فرآیندهای صنعتی را بهینهسازی کنند. با انتخاب مواد نسوز مناسب، میتوانند عملکرد فرآیندها را بهبود بخشند، هزینهها را کاهش دهند و بازدهی را افزایش دهند. بنابراین، آنالیز TMC تجهیزات در انتخاب مواد نسوز در صنعت آهن و فولاد نقش مهمی دارد و به مهندسان کمک میکند تا مواد مناسب را برای فرآیندها و شرایط خاص انتخاب کنند و عملکرد و بهرهوری را بهبود بخشند.
نقش جرم نسوز در کیفیت محصولات نهایی صنعت آهن و فولاد
استفاده از جرمهای نسوز در صنعت آهن و فولاد، مزایا و فواید زیادی را هم در تجهیزات این صنعت و هم در کیفیت محصولات نهایی صنعت آهن و فولاد فراهم میکنند. از مهمترین مزایا استفاده از جرم نسوز در صنعت آهن و فولاد، میتوان به موارد زیر اشاره نمود :
- حفاظت از تجهیزات در برابر دماهای بالا : جرمهای نسوز به عنوان لایهای محافظ از تجهیزات صنعتی مانند کورهها، پاتیلها کورههای بلند، تاندیشها و… در برابر دماهای بسیار بالا محافظت میکنند. استفاده از جرمهای نسوز در صنعت آهن و فولاد، باعث میشود که تجهیزات مورد استفاده در این صنعت، عمر طولانیتری داشته باشند. این میتواند هزینههای نگهداری و تعمیرات را نیز، به مراتب کاهش دهد.
- بهبود کنترل حرارتی فرآیند : با استفاده از جرمهای نسوز با کیفیت بالا در لاینینگ تجهیزات صنعت آهن و فولاد، حرارت به طور یکنواخت و کنترلشدهتری در فرآیند تولید آهن و فولاد توزیع میشود. توزیع یکنواخت حرارت، شرایط حرارتی پایدار و کنترلشدهای را فراهم میکند که این به بهبود کیفیت محصولات نهایی کمک میکند.
- کاهش آلودگی و ناخالصیها : اجرای جرمهای نسوز با کیفیت و یکپارچه در تجهیزات صنعتی، از ورود ناخالصیها و آلودگیها به فرآیند تولید فولاد جلوگیری میکنند. این امر باعث میشود که محصولات نهایی فولاد خالصتر و با کیفیتتر باشند.
- ارتقا بهرهوری انرژی : جرمهای نسوز از خاصیت عایق حرارتی خوب برخوردارند. پس جرمهای نسوز را میتوان با هدف تامین عایق حرارتی و ارتقای بهرهوری انرژی در انواع تجهیزات صنعت آهن و فولاد به کار گرفت. استفاده از جرم و قطعات نسوز، از هدر رفت حرارت جلوگیری کرده و با حفظ انرژی، بهرهوری از انرژی را در فرآیندهای تولید فولاد، ارتقا میدهند. بهرهوری صحیح از انرژی، علاوه بر کاهش هزینههای تولید، میتواند در بهبود کیفیت محصولات نهایی تولید نیز، موثر باشد.
- مقاومت در برابر شوکهای حرارتی : جرمهای نسوز، برای مقابله با سیکل و شوکهای حرارتی احتمالی در انواع کاربردها، طراحی میشوند. مقاومت جرمهای نسوز به شوک و تغییرات حرارت، عملکرد پایدار و بدون وقفه تجهیزات در معرض حرارت را تضمین و از ترک خوردن یا شکست زود هنگام لایههای مختلف تجهیزات صنعت آهن و فولاد، جلوگیری میکند. علاوه بر این، مقاومت جرمهای نسوز به شوکهای حرارتی وارده، به مراتب هزینههای تعمیر و نگهداری تجهیزات در معرض حرارت را کاهش میدهد. ویژگی مقاومت به شوک حرارتی در جرمهای نسوز، به بهرهوری هر چه بیشتر از تجهیزات صنعت آهن و فولاد و تولید محصولات نهایی با کیفیت بالاتر، کمک میکند.
- پایداری شیمیایی : جرمهای نسوز متناسب با شرایط شیمیایی حاکم بر کاربرد هدف انتخاب میشوند و میتوانند خاصیت اسیدی، قلیایی یا خنثی داشته باشند. اگر جرمهای نسوز به درستی انتخاب و استفاده شوند، پایداری شیمیایی بالایی را ارائه میدهند. این ویژگی آنها را برای مقابله با واکنشهای شیمیایی نامطلوب در شرایط دمایی بالای صنعت آهن و فولاد آماده میکند. با پایداری شیمیایی جرمهای نسوز در تجهیزات صنعت آهن و فولاد، تولید فولاد با کیفیت و خلوص بیشتری، امکان پذیر میگردد. زیرا استفاده از جرمهای نسوز پایدار در برابر حملات شیمیایی، باعث کاهش واکنشهای شیمیایی نامطلوب در دماهای بالا میشود. این کاهش واکنشهای نامطلوب، از تغییر خواص مکانیکی و شیمیایی محصول نهایی جلوگیری کرده و باعث حفظ کیفیت آن میشود.
مهمترین کاربرد جرم نسوز در صنعت آهن و فولاد
اهمیت بالای استفاده از جرم و مواد نسوز در صنایع آهن و فولاد، سبب شده است که در صنعت فولاد بخشی برای تولید مواد و جرمهای نسوز در محل وجود داشته باشد. این مکان میتواند آزمایشگاههای تحقیقاتی باشد. البته جرمهای نسوز، توسط شرکتهای مخصوص تولید و به بازار عرضه میشوند. این شرکتها به عنوان تولید کننده یا تامین کنندهی اصلی انواع مواد نسوز با ترکیبات و خواص حرارتی، مکانیکی و شیمیایی مختلف، فعالیت میکنند. لازم به ذکر است که بکارگیری از جرم و مواد نسوز در تجهیزات صنعت آهن و فولاد، ضروری و پر اهمیت است، به طوری که ساختار تجهیزات این صنعت از لایههای مختلف مواد نسوز بهره میبرند. به طور کلی، اگر بخواهیم مهمترین کاربردهای مواد نسوز در صنعت فولاد را معرفی کنیم، میتوانیم به موارد زیر، اشاره کنیم :
- کورههای ذوب : مواد نسوز در کورههای ذوب استفاده میشوند تا در برابر دماهای بسیار بالا که در این کورهها تولید میشود، مقاومت نشان دهند. آنها باید قادر باشند دمای بالا و شوک حرارتی را تحمل کرده و از آنها جلوگیری کنند که به دیواره کوره وارد شوند و آن را خراب کنند. مواد نسوز معمولاً با دوامی بالا، مقاومت در برابر خوردگی و حرارت، عایق حرارتی و مقاومت در برابر شوک حرارتی برخوردار هستند.
- کورههای آبگرم : در فرآیندهایی مانند تولید فولاد با استفاده از فرآیند آبگرم (hot-blast)، کورههایی استفاده میشود که هوای داغ را از طریق مجمعکوره (stove) میگذرانند. مواد نسوز در این کورهها برای مقاومت در برابر دماهای بالا و شوک حرارتی استفاده میشوند و میتوانند دمای هوا را تا حدود ۱۵۰۰ درجه سانتیگراد تحمل کنند.
- لولههای توزیع گاز : در صنعت فولاد، گازهایی مانند گاز طبیعی و گاز فرآوری شده برای استفاده در فرآیندهایی مانند ذوب و تصفیه استفاده میشوند. لولههای توزیع این گازها نیازمند مواد نسوز هستند تا در برابر دماهای بالا و خوردگی مقاومت کنند و از نشت گاز جلوگیری کنند.
- کورههای تصفیه : در فرآیندهای تصفیه فولاد، کورههای تصفیه مانند کوره قوس الکتریکی و کوره قوس الکتریکی آبسرد استفاده میشوند. مواد نسوز در این کورهها برای مقاومت در برابر دماهای بالا، شوک حرارتی و عملیات شیمیایی استفاده میشوند. آنها به عنوان یک باریکه (lining) محافظ برای دیواره کوره عمل میکنند و از خراب شدن دیواره کوره استفاده میکنند.
- وسایل حملونقل متحرک : در صنعت فولاد، وسایل حملونقل متحرک مانند بشکهها، لولهها و کاسههای ذوب از مواد نسوز ساخته میشوند. این وسایل باید قادر باشند در برابر دماهای بسیار بالا و شوک حرارتی مقاومت کنند و از نشت مواد ذوب شده جلوگیری کنند. مواد نسوز در ساخت وسایل حملونقل متحرک به دلیل مقاومت بالا در برابر حرارت، خوردگی و سایش استفاده میشوند.
در کل، مواد نسوز در صنعت فولاد در بسیاری از فرآیندها نقش حیاتی را ایفا میکنند. آنها مقاومت در برابر دما، شوک حرارتی، خوردگی و عملیات شیمیایی را فراهم میکنند و در نهایت به افزایش کیفیت و کارایی محصولات نهایی صنعت فولاد کمک میکنند.
چگونه میتوان جرم نسوز را خریداری نمود؟
با توجه به کاربردهای گسترده و تنوع فروش جرمهای نسوز شما میتوانید برای کسب اطلاعات بیشتر با مشاوران شرکت سازپاد تماس بگیرید تا با توجه به نتایج آنالیزهای حرارتی، مکانیکی و شیمیایی (TMC)، با کیفیت ترین و مناسبترین محصول را با قیمتی مناسب در اختیار شما قرار دهند.