صنعت آهن و فولاد، به عنوان یکی از زیرساختهای حیاتی تولیدات جهانی، نقش بسیار اساسی در توسعه و پیشرفت مختلف حوزههای زندگی انسانی ایفا میکند. این صنعت، با تمامی چالشها و پیچیدگیهای مرتبط با فرآیندهای تبدیل مواد خام به محصولات مورد نیاز بشر، مدتهاست در مرکز توجه قرار گرفته است. در این حوزه، مواد نسوز به عنوان یک مولفه اساسی در حفاظت از ساختار و بهبود کارایی تجهیزات اصلی این صنعت، نقش موثری را ایفا میکنند. در واقع، در صنعت آهن و فولاد، مواد نسوز با عملکرد قابل اطمینان، تجهیزات را در برابر شرایط حرارتی، مکانیکی و شیمیایی سخت و خطرات ذاتی در فرآیند فولادسازی حفاظت میکنند. در تولید فولاد، کورههای بلند، مبدلها، پاتیل، تاندیشها و دیگر تجهیزات صنعت آهن و فولاد با دماها و فشارهای بسیار بالا مواجه هستند. این تجهیزات نه تنها با چالشهای حرارتی، بلکه با نیروهای خورنده نیز مواجه هستند. از طرف دیگر، این تجهیزات ناچار به مقابله با احتمال سایش و ضربه در طول فرآیند تولید هستند. پس، به منظور افزایش عمر مفید این تجهیزات و افزایش بهرهوری، استفاده از مواد نسوز با ویژگیهای مناسب در ساختار آنها بسیار اساسی به نظر میرسد. این مواد نسوز با ارائه پوشش مقاوم در برابر حرارت، اثرات شیمیایی و تأثیرات مکانیکی، از هرگونه اختلال در کارکرد تجهیزات جلوگیری مینمایند. به این ترتیب، با بکارگیری مواد، قطعات یا انواع جرم نسوز، میتوان از اثرات مخرب ناشی از دما و نیروهای خورنده جلوگیری کرد و عمر کاری تجهیزات را بهبود بخشید. این راهبرد، به عنوان یک استراتژی هوشمندانه، در حفظ پایداری و افزایش بهرهوری صنعت آهن و فولاد تأثیرگذار است. در ادامه، صنعت آهن و فولاد و همچنین نقش قطعات و جرمهای دیرگداز در آن، به طور عمیقتر مورد بحث و بررسی قرار گرفته است.
نگاهی به فرآیندهای اساسی در صنعت آهن و فولاد
مواد اولیه، معمولاً هماتیت یا مگنتیت است که از معادن در سراسر جهان به دست میآید. این سنگهای آهن در کورههای بلند، بوتهسازی آهنسازی، دچار دگردیسی میشوند. کوره بلند، ساختار عظیمی است که ارتفاع آن به چندین طبقه میرسد، کوره بلند به عنوان یک راکتور حرارتی عمل میکند که در آن سنگ آهن، کک (مشتق شده از زغال سنگ) و سنگ آهک، تحت دمای بالا به آهن مذاب تبدیل میشود. گرمای شدید تولید شده در کوره، که اغلب بیش از 1600 درجه سانتیگراد است، کاهش اکسیدهای آهن را تسهیل میکند و آهن خام مذاب و پیشساز فولاد را تولید میکند.
سپس مذاب آهن خام با استفاده از پاتیلهای حمل مذاب کوره بلند، به فرآیند پالایش، انتقال داده میشوند. پالایش به دو روش اصلی یعنی کوره اکسیژن قلیایی (BOF) و کوره قوس الکتریکی (EAF) امکان پذیر است. در BOF، اکسیژن برای اکسید کردن ناخالصیها به آهن مذاب دمیده میشود، در حالی که EAF از یک قوس الکتریکی برای ذوب ضایعات فولاد بازیافت شده و تنظیم ترکیب در صورت نیاز استفاده میکند. این فرآیندها، فلز مذاب را پالایش میکنند، ناخالصیها را از بین میبرند و عناصر آلیاژی را تنظیم میکنند تا ترکیب فولادی مورد نظر حاصل شود.
هنگامی که فولاد تصفیه شد، فرآیند ریختهگری پیوسته آغاز میشود. در این روش، به طور مداوم محصولات نیمه تمام از جمله بیلت، اسلب یا بلوم، تولید میشود. فولاد مذاب به طور مداوم در قالب جریان مییابد و به شکل مستطیلی تبدیل میشود و سپس به محصولات نهایی تبدیل میشود. ریخته گری مداوم کارایی را افزایش میدهد، هزینهها را کاهش میدهد و محصول یکنواخت تر و سازگارتر را تضمین میکند.
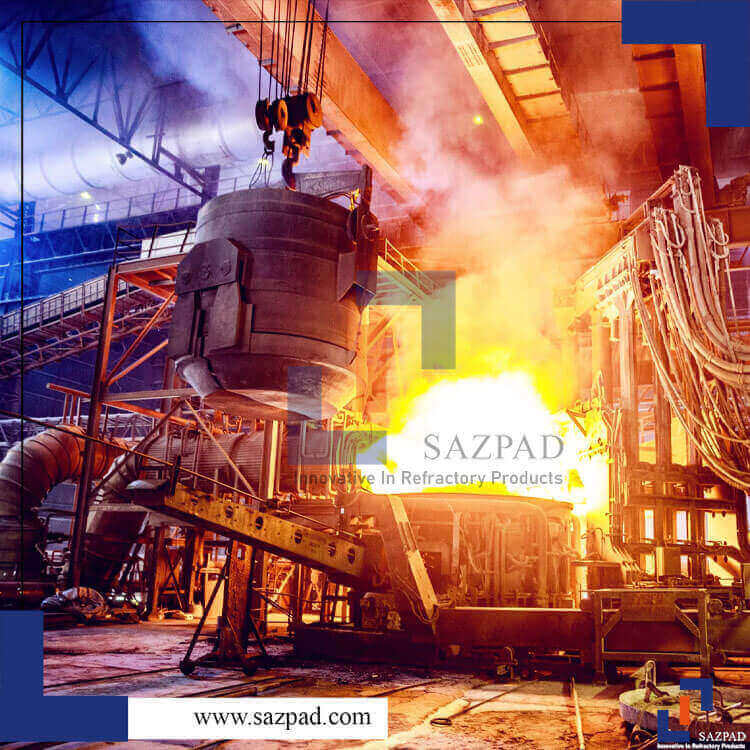
تجهیزات کلیدی در صنعت فولادسازی
تجهیزات مورد استفاده در صنعت آهن و فولاد، در فرآیندهای تولید، فرآوری و تشکیل محصولات فولادی بسیار حیاتی هستند، تا حدی که بدون آنها عملا، فرآیندی پیش نمیرود. این تجهیزات با مقاومت در برابر شرایط حرارتی بالا، فشارهای مختلف، و خصوصیات شیمیایی خاص، باید عملکرد قابل اطمینانی را در عملیاتهای تولید فولاد ارائه دهند .از اساسیترین تجهیزات مورد استفاده در صنعت آهن و فولاد، میتوان به موارد زیر اشاره نمود :
- کوره بلند یا کوره ذوب آهن : یک کوره عمودی بزرگ که در آن سنگ آهن، کک و سنگ آهک تا دمای بالا گرم میشوند. این فرآیند آهن مذاب را تولید میکند که یک محصول میانی مهم در فولادسازی است.
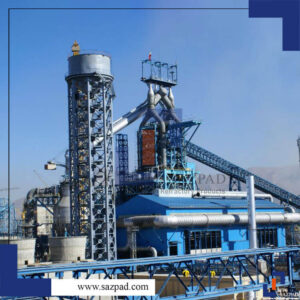
- کوره اکسیژن قلیایی (BOF) : کورهای است که برای پالایش آهن ، به فلز مذاب اکسیژن دمیده میشود. این فرآیند ناخالصیها را حذف کرده و ترکیب فولاد را تنظیم میکند.
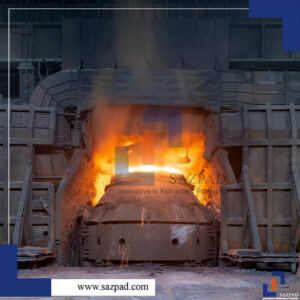
- کوره قوس الکتریکی (EAF) : یک کوره الکتریکی که ضایعات فولاد بازیافتی را ذوب میکند تا فولاد مذاب تولید شود. کورههای قوس الکتریکی به ویژه برای تولید فولادهای ویژه استفاده میشوند و نسبت به روشهای سنتی از نظر انرژی کارآمدتر هستند.
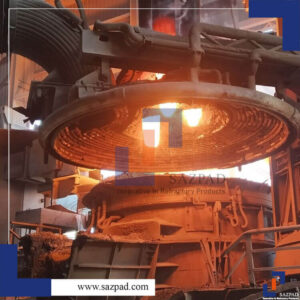
- ماشین ریخته گری پیوسته : تجهیزاتی که فولاد مذاب را در یک فرآیند مداوم به محصولات نیمه تمام (مانند بیلت، اسلب یا بلوم) تبدیل میکند. این روش کارایی و قوام محصول را بهبود میبخشد.
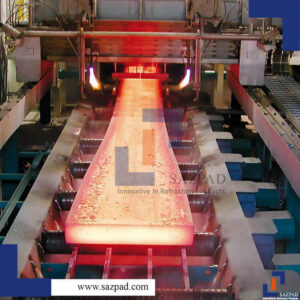
- کارخانه های نورد گرم : کارخانههای نورد که در آنها محصولات فولادی نیمه تمام حاصل از ریخته گری پیوسته از طریق یک سری فرآیندهای نورد به شکل نهایی خود در میآیند. این تجهیزات برای تولید طیف وسیعی از محصولات فولادی بسیار مهم است.
- پاتیل و تاندیشها : پاتیل و تاندیش، ظروفی مورد استفاده برای انتقال و ریختن فلز مذاب به صورت کنترل شده هستند. پاتیلها فلز مذاب را از کوره ها به ماشینهای ریخته گری حمل میکنند، در حالی که تاندیشها، جریان فلز را در طی ریخته گری مداوم تنظیم میکنند.
- کوره ها (گرم کردن مجدد و عملیات حرارتی) : کورههای گرم کردن مجدد، فولاد را قبل از پردازش بیشتر به دمای مورد نظر میرساند، در حالی که کورههای عملیات حرارتی با قرار دادن آن در چرخه های گرمایش و سرمایش کنترل شده، خواص فولاد را اصلاح میکنند.
- خطوط ترشی : خطوط مجهز به حمام اسید برای حذف ناخالصیها، فلسها و اکسیدها از سطح محصولات فولادی است. این فرآیند، فولاد را برای پردازش یا پوشش بعدی آماده میکند.
- کوره آنیلینگ : کورهای که برای بازپخت استفاده میشود، یک فرآیند عملیات حرارتی که خواص فولاد مانند سختی و شکل پذیری را با گرم کردن و خنک کردن آن در یک محیط کنترل شده تغییر میدهد.
- خطوط پوشش و پایان : خطوطی که محصولات فولادی تحت فرآیندهای پوششی مانند گالوانیزه کردن یا رنگ آمیزی برای افزایش مقاومت در برابر خوردگی یا دستیابی به خواص سطحی خاص قرار میگیرند. این خطوط به ظاهر نهایی و عملکرد فولاد کمک میکنند.
این اجزای کلیدی تجهیزات در سراسر فرآیند تولید فولاد، از استخراج مواد خام تا شکلدهی و تکمیل نهایی محصولات فولادی، پشت سر هم کار میکنند.
اهمیت آهن و فولاد در صنعت
اهمیت صنعت آهن و فولاد به فراتر از محدوده کارخانههای تولیدی میرود. این صنعت، به عنوان مبنا و اساس گسترهای از تولیدات جهانی، نقشی حیاتی در شکلدهی زیرساختها و اقتصادهای مدرن ایفا میکند. فولاد با استحکام و دوام استثناییاش، ماده اولیه در ساخت ساختمانها، پلها، جادهها و سایر پروژههای زیربنایی حیاتی است. بخشهای خودرو و حمل و نقل نیز به شدت به فولاد برای ساخت وسایل نقلیه، راهآهن، کشتیها و هواپیما متکی هستند. نسبت استحکام به وزن بالای فولاد آن را به یک ماده ایدهآل برای تضمین یکپارچگی ساختاری و ایمنی در حمل و نقل تبدیل میکند. همچنین، در بخش انرژی از طریق تولید زیرساخت برای نیروگاهها، خطوط لوله و پروژههای انرژی تجدیدپذیر، صنعت آهن و فولاد بهرهوری خود را افزایش میدهد. فولاد یک جزء ضروری در ساخت توربینهای بادی است که پایداری و طول عمر آنها را تضمین میکند. ساخت ماشینآلات و تجهیزات یکی دیگر از حوزههای کلیدی است که صنعت آهن و فولاد در آن نقش حیاتی ایفا میکند. از ماشینآلات صنعتی سنگین گرفته تا لوازم خانگی، فولاد جزء جدایی ناپذیری از تولید طیف وسیعی از تجهیزات است. به علاوه، فولاد یک ماده اساسی در ساخت کالاهای مصرفی مختلف، از جمله مبلمان، ظروف، و دستگاههای الکترونیکی است. تطبیقپذیری و دوام آن به طول عمر این محصولات کمک میکند. پس میتوان به خوبی درک کرد که صنعت آهن و فولاد، از اهمیت ویژهای برخوردار است. با این تفاصیل، پیشرفت در تکنولوژی ساخت تجهیزات مورد استفاده در صنعت آهن و فولاد، علاوه بر صرفه اقتصادی و زمانی برای کارخانهها، کیفیت محصولات نهایی را نیز افزیش میدهد. عملکرد هرچه بهتر تجهیزات، مستقیما اثر گذار است. مواد نسوز یا محصولات نسوز از جمله انواع جرمهای نسوز یکپارچه (بی شکل) و شکل دار، میتوانند به عملکرد هرچه بهتر این تجهیزات در معرض شرایط خشن حرارتی، مکانیکی و شیمیایی کمک کنند.
انواع مواد نسوز رایج در صنعت آهن و فولاد
در صنعت آهن و فولاد، در هر ناحیه از تجهیزات، بنا بر شرایط قالب بر آن ناحیه، از انواع مختلفی از مواد نسوز برای مقاومت در برابر شرایط شدید دماهای بالا، محیط های خورنده و تنش های مکانیکی استفاده میشود. در ادامه، پرکاربردترین مواد نسوز در صنعت آهن و فولاد، آورده شده است.
- جرم نسوز ریختنی : توده نسوز ریخته گری که به عنوان بتن نسوز نیز شناخته میشود، مخلوطی از پیش آماده شده از سنگدانههای نسوز، چسبانندهها و مواد افزودنی است که متناسب با نیازهای نصب به روش ریختهگری یعنی برای ریخته گری یا قالب گیری به شکلهای دلخواه، طراحی شده است. جرم نسوز ریختنی، پس از تنظیم و پخت، پوششی قوی، بادوام و مقاوم در برابر حرارت ایجاد میکند که معمولاً در محیطهای با دمای بالا مانند کورهها و سایر تجهیزات صنعتی که عایق حرارتی و مقاومت در برابر شرایط شدید ضروری است، استفاده میشود. انعطاف پذیری و سهولت کاربرد، جرم نسوز ریخته گری را به یک انتخاب همه کاره در صنایع مختلف به خصوص صنعت آهن و فولاد تبدیل میکند.
- جرم نسوز گانینگ : مخلوط دیرگداز گانینگ یا پاششی، نوعی نسوز تخصصی از گروه بزرگ دیرگدازهای بیشکل یا پودری است که از طریق دستگاه پاشش خشک به سطوح صنعتی مختلف اسپری میشود. یعنی، ماتریس دیرگداز گانینگ، به صورت مخلوطی از پیش آماده پودری و خشک به مخزن دستگاه پاشش منتقل و در نهایت، مخوط خشک از یک نازل و به طور همزمان آب از نازلی دیگر، به سطح مورد هدف پاشش میشود. پاشش این مخلوط بر روی سطوح صنعتی چون کورهها، پاتیلها و مبدلها، در نهایت به ایجاد یک پوشش مقاوم در برابر شرایط حرارتی، مکانیکی و شیمیایی خشن صنعت آهن و فولاد میپردازد. جرم نسوز یا ماتریس دیرگداز پاششی، امکان نصب سریع و کارآمد را فراهم میکند و برای تعمیر و نگهداری تجهیزات صنعتی چه در حالت گرم و چه در حالت سرد، بسیار مناسب است. جرم یا ماتریس نسوز پاششی یا گانینگ، شامل سنگدانههای نسوز (آلومینا، سیلیس و منیزیم)، چسبانندهها و مواد افزودنی است که پس از اجرا و کیورینگ، لایهای مقاوم در برابر حرارت با استحکامی بالا، ایجاد میکند. استفاده از ماتریس دیرگداز گانینگ، در صنعت به عنوان راه حل ارزان و قابل اعتماد برای بهبود پوششهای نسوز و افزایش دوام و عملکرد هرچه بهتر تجهیزات، شناخته میشود.
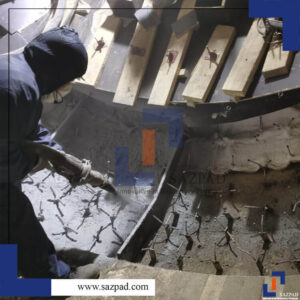
- جرم نسوز شاتکریت : جرم نسوز شاتکریت، به عنوان یک نوع مخلوط دیرگداز، به مواد نسوز خاصی اشاره دارد که از طریق پروسه پاشش تر به کار میروند. این فرآیند شامل آماده سازی یک مخلوط پودری و خشک نسوز شاتکریت با آب یا مایعی دیگر، انتقال به مخزن دستگاه گانینگ تر و پاشش از طریق یک نازل به سمت سطوح مورد هدف است. این تکنیک در صنایعی مانند آهن و فولاد که به تجهیزات مقاوم در برابر حرارت، تنش مکانیکی و انحلال شیمیایی و خوردگی نیاز دارند، استفاده میشود. نسوزهای شاتکریت اغلب مبتنی بر عناصر نسوزی چون آلومینا، سیلیس و منیزیم هستند و با چسبها و افزودنیهای دیگر ترکیب میشوند. ترکیبات جرم نسوز شاتکریت، دقیقاً کنترل میشود تا در شرایط صنعتی چالشبرانگیز، عملکرد بهینهای داشته باشد. استفاده از جرم نسوز شاتکریت، سریع و کارآمد بوده و مناسب برای تعمیر و نگهداری در شرایط گرم و سرد است. جرم نسوز شاتکریت، به عنوان یک راه حل، بهبود ماندگاری و بهینهسازی پوششهای نسوز در تنظیمات صنعتی مختلف را فراهم میکند و در کاهش زمان خرابی و افزایش راندمان عملیاتی صنعت موثر است.
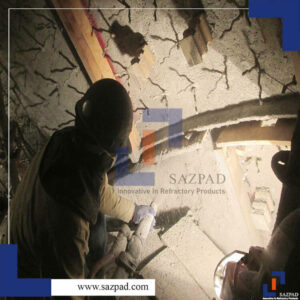
- جرم نسوز کوبیدنی : مخلوط دیرگداز کوبشی، ترکیبی از مواد یا اجزای نسوزی چون آلومینا، منیزیم و سیلیس در کنار بایندرها و مواد افزودنی است که دانهبندی و خواص آن مطابق با روش نصب کوبیدن و متراکم کردن، طراحی شده است. ماتریس نسوز کوبیدنی، عمدتا با استفاده از چکشهای دستی و یا چکشهای پنوماتیک، به صور خشک یا نیمه مرطوب، در جای خود کوبیده میشوند و بسته به نیازهای کاربرد مورد هدف، به دو روش هواسخت و گرماسخت، پخته، عمل آوری یا تنظیم میشوند. ماتریسهای نسوز رمینگ، پس از تنظیم، پوششی یکپارچه، متراکم، با دانسیته بالا و حداقل تخلخل را نتیجه میشوند. جرم نسوز کوبشی، عمدتا در ساخت لایه ایمنی، کف یا در پر کردن شکافهای موجود در تجهیزات صنایع در معرض حرارت بالا، من جمله صنعت آهن و فولاد، بسیار کاربردی هستند.
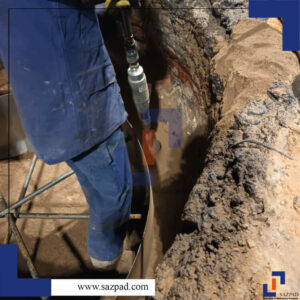
- آجر نسوز : آجرهای نسوز، از اساسیترین و یا میتوان گفت رایجترین محصولات دیرگداز مورد استفاده در صنایع متعدد به خصوص صنعت آهن و فولاد است که اغلب آلومینایی، منیزیایی یا سیلیسی هستند. آجرهای دیرگداز، بسته به عنصر پایه تشکیل دهندهاش، مشخصات حرارتی، مکانیکی و شیمیایی متنوعی را ارائه میدهند. نوع آجرهای نسوز، مثل دیگر از انواع محصولات نسوز، بر اساس آنالیز TMC (آنالیز حرارتی، مکانیکی و شیمیایی) کاربرد مورد نظر و همچنین خاصیت سرباره موجود (اسیدی یا قلیایی)، انتخاب میشود. آجرهای نسوز، تقریبا در تمامی نواحی تجهیزات صنعتی در معرض حرارت، از جمله کف، دیواره و… قابل استفاده است. به طور کلی آجرهای نسوز، میتوانند دماهای بسیار بالا و ضربات و سایشهای احتمالی را تحمل و در برابر انحلال شیمیایی و خوردگی نیز مقاومت بسیار عالی را ارائه دهند. پس تنها باید به درستی و متناسب با نیازهای کاربرد، انتخاب شوند. آجرهای نسوز، با استفاده از ملات و یا بدون آن، توسط آجرچینهای ماهر اجرا میشود. ملات نسوز در آجر چینی، با بستن درزهای موجود، از نفوذ مواد مذاب جلوگیری میکند. اما در حالت بدون ملات نسوز نیز، به دلیل انبساط حرارتی آجر نسوز، آجرها خود در جای خود چفت میشوند. از اینرو، تنها در مواردی که نیاز به آزادسازی تنشهای حرارتی است، از ملات نسوز در نصب آجرهای نسوز استفاده میشود.
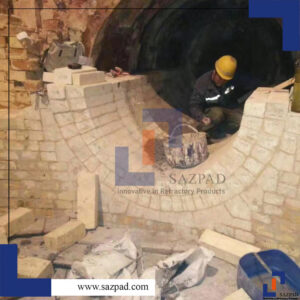
- قطعات پیش ساخته نسوز : قطعات نسوز یا دیرگداز از پیش ساخته (refractory prefabricated parts)، اجزای از پیش مهندسی شدهای هستند که در صنایع در معرض حرارت به خصوص صنعت آهن و فولاد برای افزایش کارایی و طول عمر تجهیزات حیاتی در معرض دماهای شدید و شرایط سخت استفاده میشوند. این اشکال پیش ساخته که از موادی مانند آلومینا بالا، سیلیس، منیزیم و سایر ترکیبات نسوز تخصصی ساخته شدهاند، اهداف مختلفی را در کاربردهای مختلف انجام میدهند. از پاتیلها و تاندیشها گرفته تا آسترهای کوره و تجهیزات ریخته گری، این قطعات نسوز از پیش ساخته مزایایی مانند نصب آسان، کاهش زمان خرابی و عملکرد ثابت را ارائه میدهند. آنها نقش مهمی در بهینه سازی پوششهای نسوز، بهبود راندمان حرارتی و به حداقل رساندن سایش و فرسایش در طول تولید و فرآوری فلز مذاب دارند. قطعات نسوز پیش ساخته چه برای مقاومت در برابر ضربه، عایق حرارتی یا راه حلهای سفارشی طراحی شده برای هندسههای پیچیده استفاده شود، به طور قابل توجهی به قابلیت اطمینان و کارایی فرآیندهای فولادسازی کمک میکند. قطعات نسوز پیش ساخته، نسبت به انواع جرمهای نسوز بیشکل، عملکرد و مشخصات قابل پیشبینیتری را ارائه میدهند. چرا که، این قطعات دیرگداز، از قبل در کارخانه با نسبت ثابت مواد و در شرایط کنترل شده، ساخته میشوند. بنابراین، استفاده از قطعات نسوز پیشساخته، دیگر خطاهای نصب و حتی خطاهای آمادهسازی انواع جرمهای نسوز بیشکل را نداشته و بهطور مستقیم از تجربه و دقت مهندسان در فرآیند ساخت بهره میبرند. قطعات نسوز پیش ساخته، با تضمین کیفیت و یکنواختی در تولید، به سرعت و با دقت در محل نصب قرار گرفته و بر خلاف جرمهای نسوز بیشکل یا پودری، نیازی به زمان زیاد برای آمادهسازی و نصب ندارند. به کارگیری قطعات نسوز پیشساخته، نهتنها هزینهها و زمانهای توقف تولید را کاهش میدهد، بلکه اطمینان از کارکرد بهتر و موثرتر تجهیزات در محیطهای با دماها و شرایط سخت صنعتی را نیز ارتقاء میبخشد.
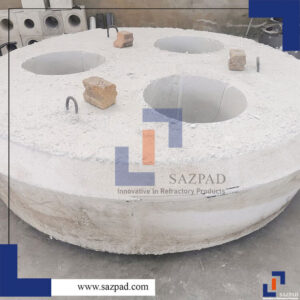
نسوز مناسب در حاملهای مذاب کوره بلند
مواد نسوز مورد استفاده در قسمتهای مختلف در حاملهای مذاب کوره بلند (مانند پاتیل و رانر) بر اساس شرایط و نیازهای خاص هر ناحیه متفاوت است. در ادامه، برخی از مواد نسوز رایج مورد استفاده برای قطعات مختلف آورده شده است :
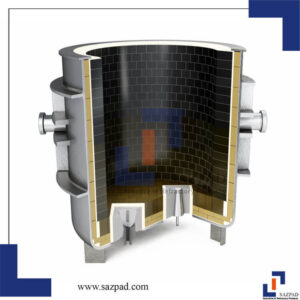
آستر پاتیل حمل مذاب
آجرهای نسوز با آلومینا بالا یا آجرهای نسوز کربن منیزیمی اغلب برای ساخت آستر پاتیل استفاده میشود. این مواد در برابر دماهای بالا (1400 الی 1600 درجهسانتیگراد که همان دمای فلز مذاب است) و خوردگی یا انحلال شیمیایی مقاومت میکنند. این خواص برای نگهداری و انتقال فلز مذاب بسیار مهم است. توجه داشته باشید، نوع سرباره اسیدی یا قلیایی موجود، از کلیدیترین مشخصهها در انتخاب نسوز مصرفی است. از ماتریسهای دیرگداز ریختهگری و جرمهای نسوز شاتکریت با ویژگیهای مشابه نیز میتوان استفاده نمود.
آستر تاندیش
آجرهای نسوز یا جرمهای نسوز ریختنی مبتنی بر آلومینا-گرافیت، آندالوزیت، مولایت و یا منیزیم معمولاً در آسترهای تاندیش استفاده میشوند. این مواد مقاومت خوبی در برابر دمای بالا (1400 الی 1600 درجهسانتیگراد که همان دمای فلز مذاب است)، شوک حرارتی و در برابر فرسایش دارند و عملکرد پایدار را در طول فرآیند ریختهگری تضمین میکنند.
پد یا بالشتک ضربه و دلتا
قطعات نسوز پیش ساخته آندالوزیتی، مولایتی و یا منیزیایی بالا در پد یا بالشتکهای ضربهگیر و دلتا پاتیل مناسب است. این اشکال به مقاومت در برابر ضربه فلز مذاب در هنگام ریختن کمک میکند و از سایش و فرسایش نیز جلوگیری میکند.
نازل و شرودهای ریختهگری
نسوزهای آلومینا-کربن یا منیزیم-کربن اغلب برای ساخت نازل و شرودهای ریختهگری در پاتیلها استفاده میشوند. این دسته از مواد نسوز، در برابر دمای مذاب فولاد که تقریبا 1600 درجهسانتیگراد است، بسیار مقاوم هستند. به علاوه، به دلیل انعطافپذیری عالی، میتوانند سیکل حرارتی وارده در این ناحیه را به خوبی تحمل کنند. از طرفی، بسته به ناحیه و میزان اثرات مکانیکی، با کم یا زیاد کردن کربن، مقاومت مناسب و متعادلی را در برابر نیروهای سایشی و ضربات وارده ارائه میدهند.
ست ول بلوک
ست ول بلوک در تاندیشها ممکن است از منیزیم یا منیزیم-کروم نسوز استفاده کنند. این مواد در برابر حملات شیمیایی و پایداری حرارتی مقاومت دارند.
توجه!!! توجه به این نکته مهم است که انتخاب مواد نسوز به عواملی مانند دما، ترکیب شیمیایی فلز مذاب و نیازهای خاص هر کاربرد بستگی دارد. هدف انتخاب موادی است که بتواند در شرایط سخت مقاومت کند و طول عمر و قابلیت اطمینان پوششهای نسوز را در حاملهای مذاب کوره بلند فراهم کند. مواد نسوز خاص مورد استفاده میتواند در میان تاسیسات مختلف فولادسازی بر اساس ترجیحات، تجربیات و ماهیت عملیات آنها متفاوت باشد. بدین منظور، نیاز است تا قبل از تهیه هرگونه متریال نسوز، گزارشی از آنالیز TMC (thermal , mechanical & chemical analysis) کاربرد مورد هدف تهیه و بر اساس آن، مواد نسوز متناسب با نیازهای هر ناحیه، انتخاب و استفاده شود.
نسوز مناسب در کنورتور یا کوره اکسیژن قلیایی (BOF)
در مبدلها یا کورههای اکسیژن پایه (BOF) که در آنها، وظیفه اصلی تبدیل آهن مذاب به فولاد است، مواد نسوز مورد استفاده باید در برابر دماهای شدید، واکنشهای شیمیایی و تنشهای مکانیکی مقاومت کنند. در ادامه، مواد نسوز مناسب نواحی کلیدی یک BOF آورده شده است :
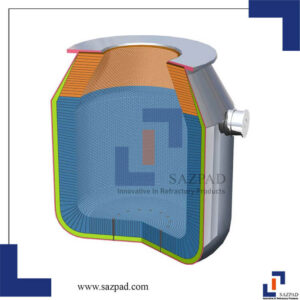
ناحیه مخروطی پایینی BOF (استادیوم)
اغلب در ناحیه استادیوم کنورتور از آجرهای نسوز منیزیا-کربن، استفاده میشود. این مواد نسوز در برابر دماهای بالا (1400 الی 1600 درجهسانتیگراد که همان دمای فلز مذاب است) و اثرات مکانیکی چون سایش و ضربه، مقاومت میکنند. بنابراین، برای ناحیه استادیوم کوره اکسیژن قلیایی که عملا در معرض دمای بالا، سیکل گرمایش و سرمایش متوسط، تنشهای مکانیکی چون سایش و ضربه و همچنین انحلال شیمیایی ناشی از سرباره قلیایی قراردارند، آجرهای نسوز منیزیا – کربنی، میتواند موثر باشد.
ناحیه مخروطی بالایی BOF
در قسمت مخروطی بالایی کنورتور، با توجه به تنشهای حرارتی ناشی از دمای 1400 الی 1600 درجه سانتی گراد مذاب، سیکل گرمایش و سرمایش، ضربات ناشی از لنس زنی برای تمیزکاری دهانه، سایش ناشی از گازهای فرآیند و انحلالهای شیمیایی ناشی از سرباره قلیایی، لازم است تا از آجر نسوزی با ویژگیهای متناسب با این شرایط استفاده شود. آجرهای نسوز منیزیا – کربنی، میتوانند نیازهای ناحیه مخروطی بالایی کوره اکسیژن قلیایی را ارضا نمایند. در قسمت دهانه نیز میتوان از جرمهای گانینگ، پلاستیک و شاتکریت منیزیایی و دولومیتی استفاده نمود.
لایه کاری ایمنی BOF
در لایه ایمنی کنورتور، شدت تنش حرارتی، سیکل حرارتی، اثرات مکانیکی و انحلال یا خوردگیهای شیمیایی، نبست به دیگر لایههای تشکیلدهنده BOF، کمتر است. بدین منظور، آجرهای نسوز ارزان همچون آجرهای نسوز منیزیا زینتری میتوانند برای سالیان سال، کارآمد باشند. توجه داشته باشید که از جرمهای نسوز شاتکریت نیز میتوان در لایهکاری ایمنی کنورتور، استفاده نمود. در بسیاری از موارد، استفاده از جرم نسوز شاتکریت، بهترین گزینه است اما باید به تعبیه درز انبساط ، انکرگزاری و همچنین دقت و احتیاط در نصب، پرداخته شود.
دیواره تخلیه BOF
دیواره تخلیه کنورتور یا کوره اکسیژن قلیایی (Basic Oxygen Furnace)، دیوارهای است که مذاب در حین تخلیه، بر روی سطح آن قرار میگیرد. در حین تخلیه مذاب، به مدت 3 الی10 دقیقه، دمای این ناحیه بین 1500 الی 1700 درجه سانتیگراد، متغییر است. از طرفی، با توجه به تعداد ذوب گیری در روز، سیکل گرمایش و سرمایش (چرخه حرارتی) در این ناحیه متوسط است. در دیواره تخلیه کنورتور، اثرات مکانیکی از جمله ضربه یا سایش نیز چندان معضل نیستند. با این تفاصیل، در دیواره تخلیه، آجرهای منیزیا – کربنی، میتوانند عملکرد بسیار خوبی را در برابر اثرات حرارتی، مکانیکی و شیمیایی حاکم بر این ناحیه را نشان دهند.
دیواره بارگیری BOF
اگر دمای 1500 الی 1700 درجه سانتیگرادی، سیکل گرمایش و سرمایش زیاد، ضربات و سایشهای وارده ناشی از شارژ قراضه، انحلال شیمیایی و خوردگی ناشی از سرباره، در هنگام انتخاب نسوز تشکیل دهنده دیواره بارگیری BOF، در نظر گرفته نشوند، علاوه بر پدیدار شدن آسیبهای جبران ناپذیر، عملکرد کنورتور نیز، عملا متوقف خواهد شد. در چنین شرایطی، استفاده از آجرهای نسوز 100 درصد منیزیای ذوبی یا حاوی 15 الی 20 درصد کربن، میتواند به خوبی به نیازهای فوق، پاسخ دهد.
ترنیون BOF
قسمت شکم کنورتور، باید برای مقابله با دمایی معادل دمای مذاب فولاد، سیکل گرمایش و سرمایش متوسط، سایش اندک ناشی از تلاطم مذاب، انحلال شیمیایی و خوردگی ناشی از سرباره، ساخته شود. در ساخت ترنیون کنورتور، استفاده از آجرهای نسوز منیزیا– کربنی، بهترین گزینه است.
لایه کاری کف BOF
در عملیات لایه کاری کف کوره اکسیژن قلیایی (BOF)، باید از موادی نسوز با تحمل دمای تقریبا 1700 درجه سانتیگراد و مقاوم در برابر شوکهای حرارتی زیاد، تنشهای مکانیکی ناشی از شارژ قراضه و تلاطم مذاب و سازگار با سرباره، استفاده شود. آجرهای منیزیا – کربن، قادرند که نیازهای کف کنورتور را به خوبی برآورد کنند. آنها با سرباره قلیایی موجود در کنورتور سازگارند و از انحلال شیمیایی یا خوردگی، جلوگیری میکنند.
تپ هول BOF
مجرای خروجی کنورتور یا لتکا که برای خروج مذاب فولاد پالایش شده از کنورتور، استفاده میشود، از سه ناحیه بلوک بیرونی مجرا، پرکننده یا جرم ریختنی و آستر داخلی مجرا، تشکیل میشود. در قسمت بلوک بیرونی، دما به دمای مذاب فولاد میرسد و تنها در زمان تعویض آستر، ممکن است شوک حرارتی و ضربه برای این ناحیه، معضل محسوب شود. در قسمت آستر داخلی نیز، دما به 1500 الی 1700 درجه سانتیگراد رسیده و شوک حرارتی نیز بسته به تعداد ذوب، تقریبا زیاد است. از طرفی، آستر داخلی تپ هول، ممکن است در حین تلاطم مذاب و همچنین تمیزکاری، به ترتیب اثرات مکانیکی چون سایش و ضربه را تجربه کنند. با این تفاصیل، بلوک بیرونی میتواند از مواد نسوز منیزیا زینتری – گرافیتی باشد. از طرفی، مواد نسوز منیزیای ذوبی – کربنی نیز در آستر سازی داخلی تپ هول، به طور موثر و کارآمد، قابل استفاده هستند. توجه داشته باشید که ناحیه پرکننده یا جرم ریختنی، میتواند با استفاده از جرم نسوز کوبیدنی منیزیا بدون کربن، انتخاب شود.
نسوز مناسب کوره قوس الکتریکی (EAF)
کوره قوس الکتریکی (EAF)، نوعی کوره است که از یک قوس الکتریکی برای گرم کردن و ذوب قراضه، استفاده میکند. فناوری اصلی کوره قوس الکتریکی بر اساس الکتریسیته و با استفاده از الکترودها است که دما را در نوک الکترود به 3000 درجه سانتیگراد میرساند و در نهایت قراضه و آهن، در این دما ذوب میشود. از طرفی، انرژی شیمیایی از طریق تزریق اکسیژن و یا گازهای طبیعی، در طی فرآیند به ذوب شدن کمک میکند. کوره قوس الکتریکی (EAF)، از مناطق مختلفی تشکیل شده است که هر کدام به دلیل شرایط سخت و تغییرات دما به مواد نسوز خاصی نیاز دارند. در ادامه مناطق اصلی در یک EAF و مواد نسوز مناسب برای هر یک آمده است :
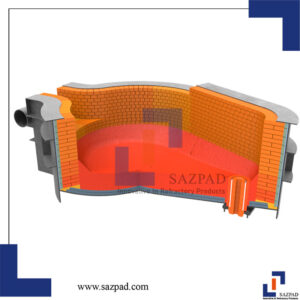
لایه کاری ایمنی EAF
در صورت تخریب لایهکاری اصلی دیواره داخلی، ممکن است دمای لایه ایمنی کوره قوس الکتریکی به 1400 درجه سانتیگراد نیز، برسد. در چنین شرایطی، تلاطم مذاب نیز میتواند تنشهای سایشی را در این ناحیه رقم بزند. از طرفی تنها در حین تمیزکاری ممکن است به لایه ایمنی ضربه وارد شود. پس، آجرهای نسوز ارزان قیمتی چون آجر نسوز منیزیا زینتری، در این ناحیه به عنوان بهترین گزینه شناخته میشوند. این دسته از آجرهای نسوز، پایدارند و برای سالیان سال، به طور کارآمد، عمل میکنند. در لایه کاری ایمنی، جرمهای نسوز ریختنی ویبره شونده و جرمهای نسوز پلاستیک نیز، قابل استفاده هستند.
لایه کاری کف EAF
تجربه نشان داده که استفاده از جرمهای کوبیدنی ویبره شونده خشک در کف کورههای قوس الکتریکی، نسبت به آجرهای نسوز، از نظر نصب و عمر مفید، عملکرد بهتری را ارائه میدهند. در ناحیه کف کوره قوس الکتریکی، دما به 1650 درجه سانتیگراد نیز میرسد. به علاوه، شوک حرارتی وابسته به تعداد ذوب روزانه و تخلیه هفتگی مذاب است، بنابراین با توجه به شرایط اپراتوری، شدت شوک حرارتی متفاوت است، اما نسوز مورد استفاده در این ناحیه باید بر مبنای احتمال شوک حرارتی زیاد، طراحی شود. از طرفی، مواد نسوز این ناحیه باید توان مقابله با ضربات ناشی از شارژ قراضه و تنشهای سایشی ناشی از لنس زدن، دمش گاز آرگون و دمش اکسیژن، را داشته باشند. جرم نسوز کوبشی منیزیا – آهک، با تکیه بر واکنشهای شیمیایی منیزیم با آهک، میتواند تمامی شرایط خشن ذکر شده را به خوبی تحمل کند. پس، بهترین گزینه است.
لایه کاری دیواره EAF
لایه کاری دیواره کوره قوس الکتریکی از چهار ناحیه اساسی از جمله آجرهای بالای مجرای خروجی، آجرهای نقطه داغ، آجرهای دیواره اصلی و آجرهای ناحیه درب کوره تشکیل شده است. دیواره کوره قوس الکتریکی در کلیه نواحی، باید برای مقابله با دمای 1600 الی 1700 درجه سانتیگراد، سیکل گرمایش و سرمایش، ضربات و سایشهای وارده به خصوص در ناحیه درب شارژ کوره (در ناحیه درب شارژ کوره، ضرباتی ناشی از تمیزکاری و سایشهای ناشی از عبور سرباره، رخ میدهد.) و انحلال شیمیایی و خوردگی ناشی از سرباره، طراحی شود. در ناحیه درب کوره و دیواره پایینی، آجرهای نسوز متشکل از 95 درصد منیزیا زینتری و 5 درصد کربن مناسب هستند. در دیواره پایینی و ناحیه داغ، آجرهای منیزیم ذوبی حاوی 10 الی 15 درصد کربن، مقاوت حرارتی، مکانیکی و شیمیایی مورد نیاز این ناحیه را تامین میکنند.
سیستم دمش گاز آرگون EAF
پرج پلاگ یا سیستم دمش آرگون از سه جزء بلوک پیرامونی، توپی دمش و بلوک نگهدارنده تشکیل شده است. در پرج پلاگ، حداکثر دما، معادل با دمای فولاد مذاب است. از طرفی، با توجه به اینکه سطح توپی دمش، گاز نسبتا سرد را وارد کوره میکند و همزمان نیز با مذاب داغ در تماس است، شوک یا سیکل حرارتی این ناحیه بسیار زیاد است. به علاوه، ضرباتی با شدت متوسط در حین شارژ قراضه به توپی دمش گاز آرگون وارد میشود. توپیهای دمش گاز آرگون در کوره قوس الکتریکی، تحت اثرات نیروها یا تنشهای سایشی زیاد هستند. بدین منظور در سیستم دمش گاز آرگون، توپی دمش از 20 لوله از جنس فولاد که در یک قطعه پیش ساخته منیزیا – کربنی پرس شده است، استفاده میشود. بلوک نگدارنده در این سیستم نیز، عمدتا قطعهای پیش ساخته منیزیا – گرافیتی است.
دلتای سقف EAF
دلتای سقف کوره قوس الکتریکی، قطعهای نسوز است که بین الکترودهای اصلی و سقف کوره قرار میگیرد و از جهش جریان الکتریکی به سقف و ایجاد قوس در بیرون از کوره جلوگیری میکند. به علاوه، امکان عبور الکترودها از میان دلتا بدون داشتن فضای خالی زیاد برای فرار گازها را نیز فراهم میکند. دمای این ناحیه، میتواند به اندازه 50 درجه سانتیگراد بیشتر از دمای مذاب فولاد نیز برسد. به علاوه، با توجه به قرارگیری دلتا در مرکز سقف و تماس مستقیم آن با حرارت ناشی از فرآیند ذوب، سیستم خنک کننده با آب در کنارهها و همچنین تماس کوره با هوا از بالا، شوک حرارتی در این ناحیه، بسیار زیاد است. از طرفی، در حین فرآیند ذوبگیری، گازهای داغ ناشی از فرآیند به دلتا برخورد کرده و از میان آن عبور میکند. این منجر به ایجاد تنش سایشی میشود. به علاوه، وجود سرباره و حضور گازهای داغ نیز، شرایط انجام واکنشهای شیمیایی را نیز فراهم میکند. پس نسوز مورد استفاده در این ناحیه باید در برابر شرایط ذکر شده، ظرفیت بالایی را ارائه دهد. بدین منظور، دلتای سقف مصرفی عمدتا از جنس آلومینا و مقداری زیرکونیا برای افزایش مقاومت به شوک حرارتی است. توجه داشته باشید که در فاصله بین رینگهای خنک کننده و دلتا باید از جرم ریختنی یا قطعه نسوز پیش ساخته و یا کاغذ یا پتو نسوز، به منظور تعبیه درز انبساطی استفاده نمود.
مجرای خروج مذاب EAF
تپ هول در کوره قوس الکتریکی از چهار جزء اساسی یعنی بلوک محافظ بیرونی، پر کننده، آستر و بلوک انتهایی تشکیل میشود و در نهایت در کف کوره، به منظور تخلیه قابل کنترل مذاب و جلوگیری از ورود سرباره اضافی به پاتیل حمل مذاب، نصب میشود. در آستر داخلی و بلوک انتهایی تپ هول، دما بین 1600 الی 1700 درجه سانتیگراد متغییر است. به علاوه، با توجه به تعداد ذوب گیری روزانه و سرد و گرم شدن آستر، شوک حرارتی در این ناحیه بسیار زیاد است. اما در بلوک انتهایی، به دلیل قرار گیری بلوک در معرض هوای بیرون، این وضعیت بدتر است. از طرفی، به بلوک انتهایی با هر بار باز و بسته شدن دریچه به صورت رف و برگشتی و همچنین در حین تمیزکاری زوائد فولاد و سرباره، ضربه وارد میشود. تلاطم مذاب نیز، میتواند در این ناحیه، تنشهای سایشی مخربی را تحمیل کند. علاوه بر این موارد باید توجه شود تا در این ناحیه، از مواد نسوزی سازگار با سرباره، استفاده شود تا از انحلال و یا خوردگی شیمیایی، جلوگیری شود. بدین منظور است که در آستر داخلی تپ هول کوره قوس الکتریکی، از نسوزهای منیزیا کربنی، در بلوک انتهایی از قطعات نسوز آلومینا- سیلیکون کربید– کربن، در بلوک محافظ از نسوزهای منیزیا کربنی و در نهایت از جرم کوبیدنی در حالت سرد و جرم پاشیدنی یا گانینگ منیزیایی در حالت گرم به منظور تکمیل ناحیه پرکننده، استفاده میشود.